When it comes to injection molding, we do ‘difficult’ every day.
"*" indicates required fields
- Years of experience working with challenging materials, processes, and complex inspections involved in highly regulated industries
- Our seasoned experts provide best-in-class engineering support, including design for manufacturability (DFM), predictive engineering, and Moldflow® simulation to optimize mold design, improve efficiency, lower cost, and reduce lead time
- We use scientific molding principles and advanced molding technology such as Kistler sensors, systems, and software solutions for quality assurance.
Tailored solutions for complex requirements.
Insert molding
Insert molding is a process that involves an insert, typically metal, that is placed in the tool for injected plastic to flow around. Encapsulating the insert with plastic eliminates an assembly step to create a single molded plastic piece that’s generally stronger and lower cost than one created using secondary assembly. The insert can be loaded into the mold manually or with automation, which minimizes human error, improves efficiencies, and ensures optimal cycle times.
Overmolding
Overmolding typically involves a rigid, plastic-based substrate overlaid with a pliable, rubber-like thermoplastic elastomer to create a soft-touch grip. This process results in a seamless bond of multiple materials into a single part or product.
Two-shot molding
Two-shot molding (also called dual-shot, double-shot, multi-shot), is a process in which two different plastic resins are molded together in a single machining cycle. Two-shot molding is typically used when production demand is too high for overmolding.
In-mold decoration
In-mold decoration is an effective way to add marking, decorative or branding touches to any plastic component or device during the injection molding process rather than through an additional secondary process. It enhances chemical resistance and reduces the risk of distortion in warning labels and button artwork. Examples include text, colors, textures, and shapes. Additional benefits of in-mold decorating include streamlined production, time savings, and reduced costs.
Plastic Injection Molded Products
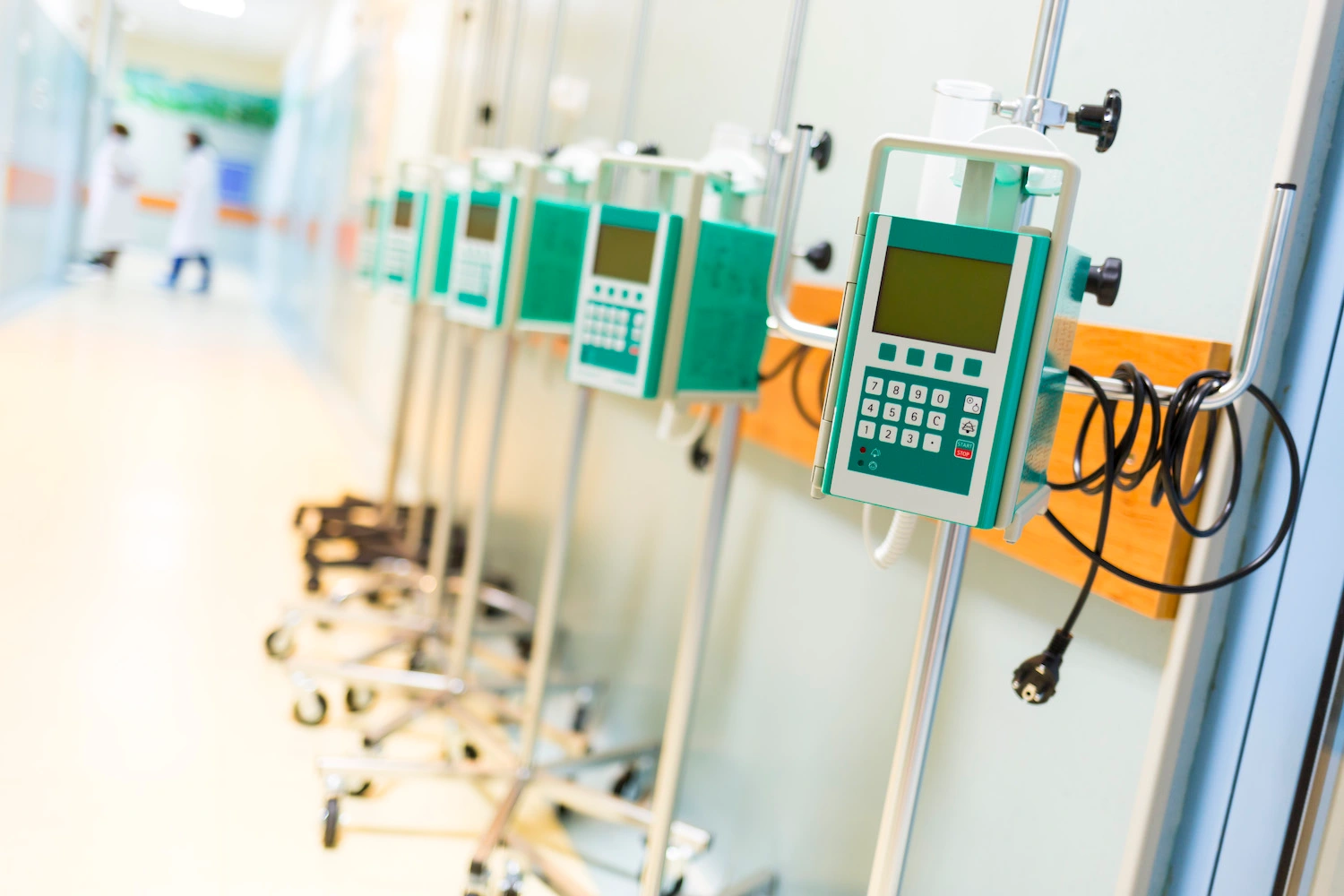
Intravenous Infusion Pump System
Aptyx optimized the design for scalable manufacturing and supplies the mission-critical gear system that precisely drives the pump module and several support components and sub-assemblies within this product.
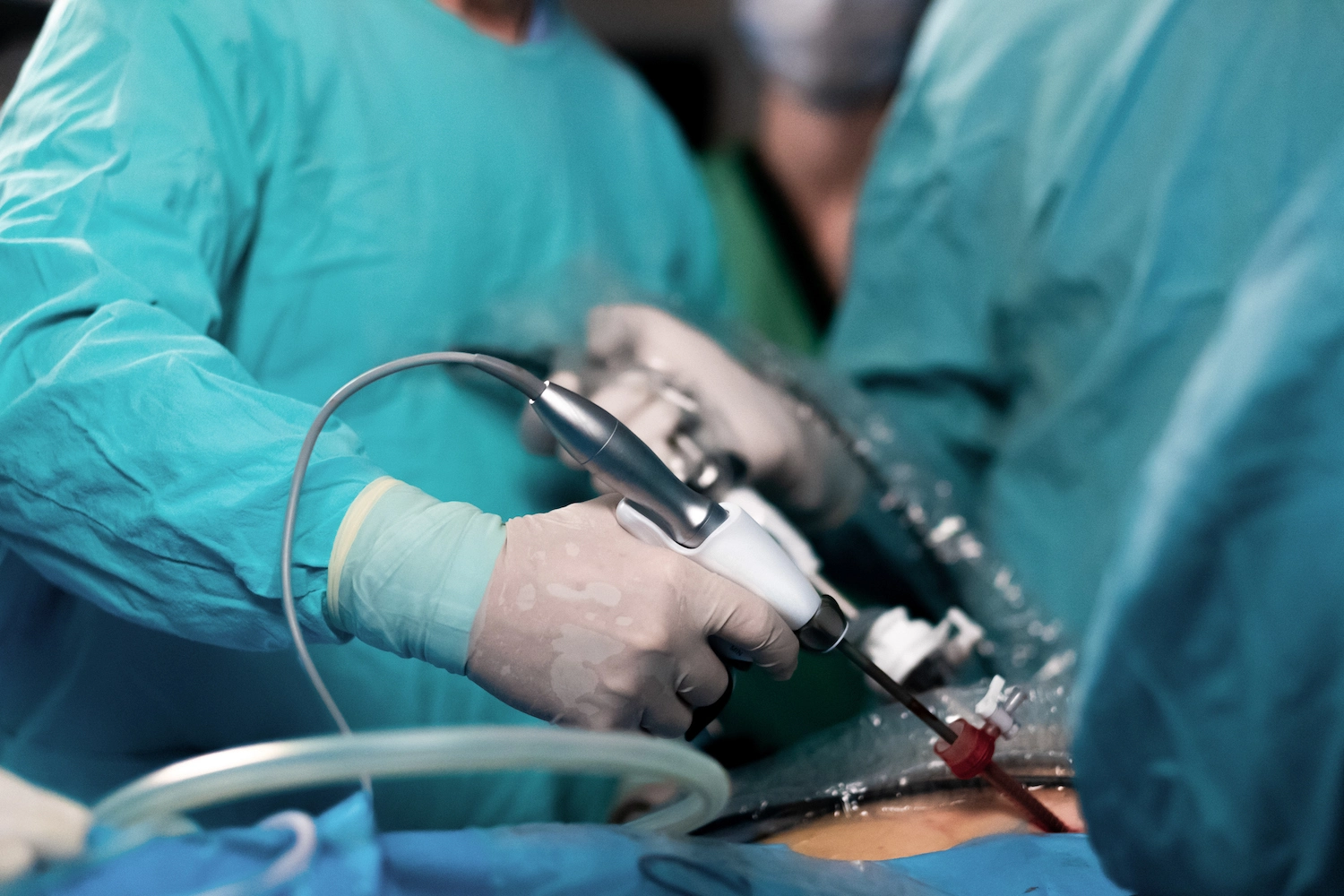
Laparoscopic Surgery Multi-tool
This minimally invasive device combines the functions of five instruments into one, powered by a planetary gear retracting system produced by Aptyx.
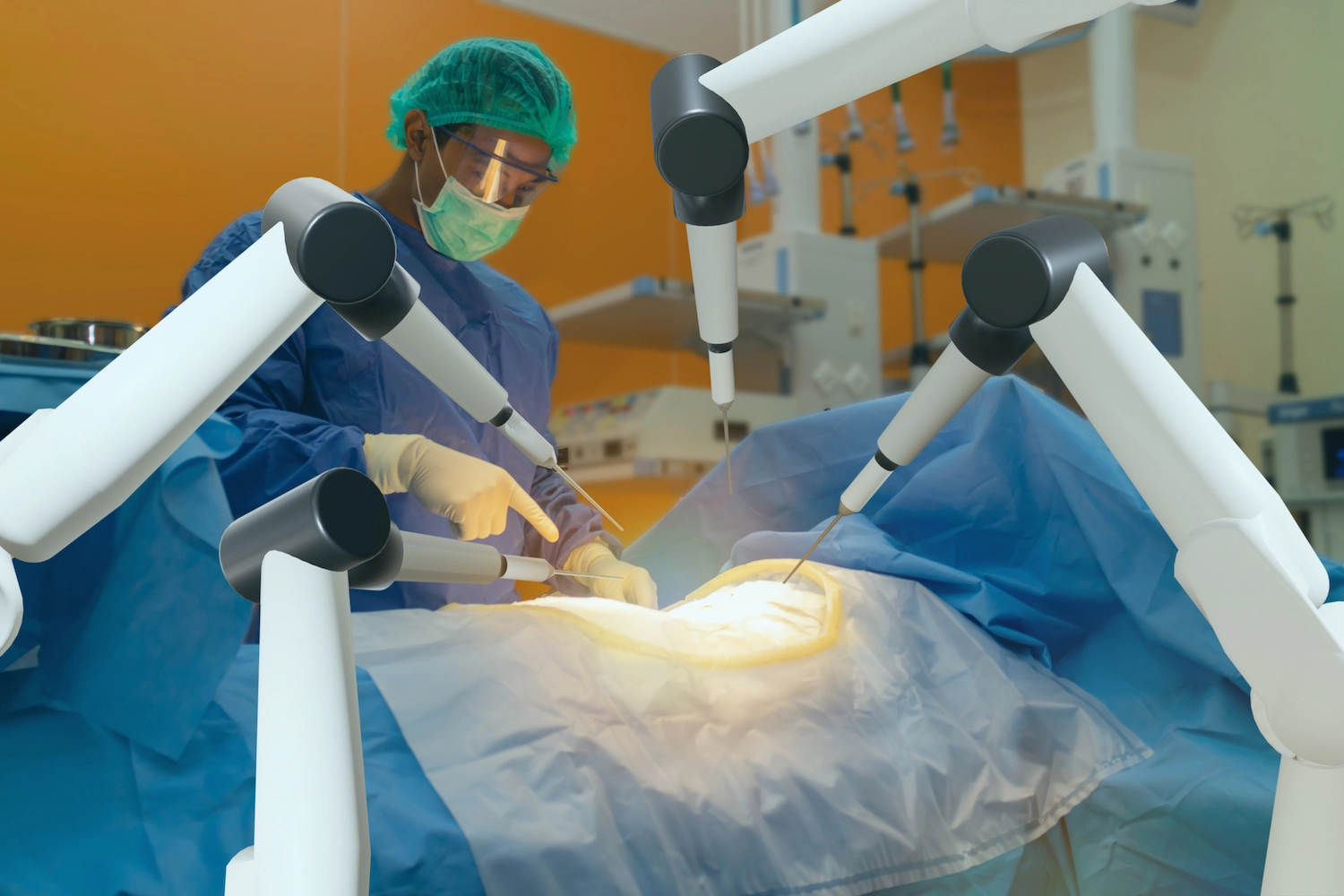
Robotic Surgery Systems
From the reusable control arms to the disposable end of arm devices, Aptyx assists in the design and tool build and produces the mechanical drive system for many of the leading robotic surgery systems.
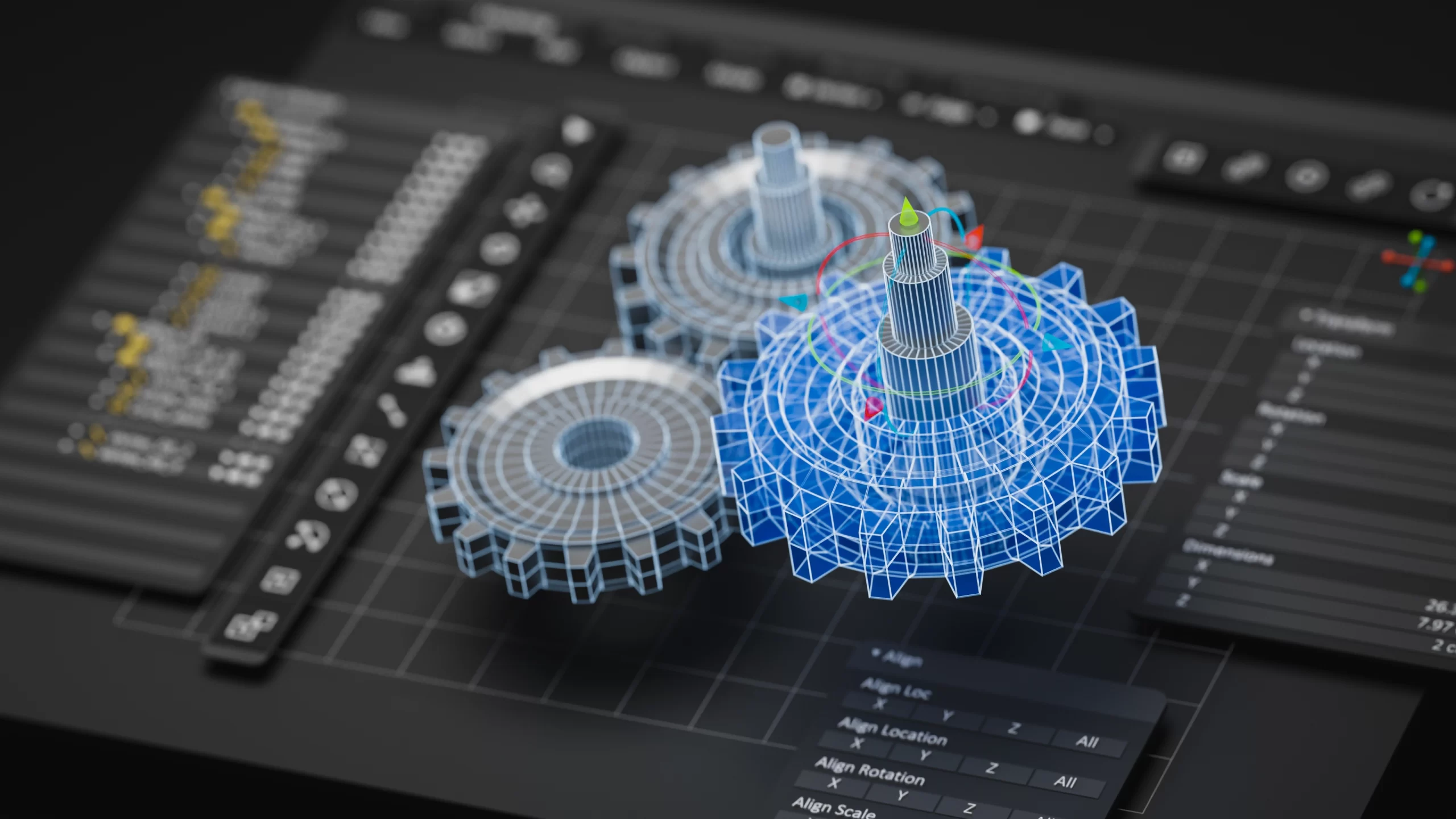
Plastic Gears
High-strength plastic gears are key to the precise functioning of various equipment used in the medical device, industrial, aerospace and defense, and energy industries. Our custom plastic injection molding solution examples include medical fluid delivery pumps, automated teller machines (ATMs), and vehicle and building HVAC equipment.
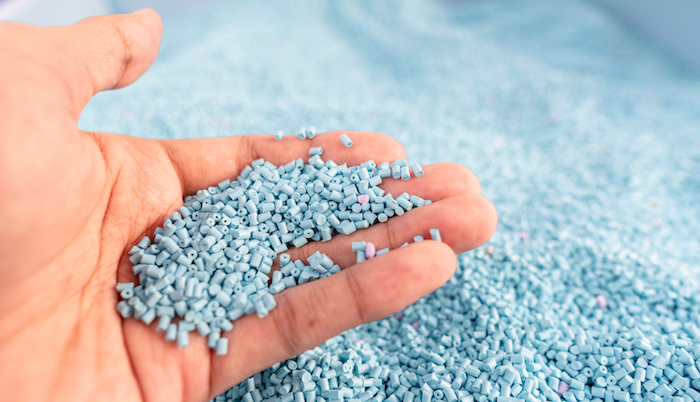
Materials expertise for plastic injection molding.
Plastic injection molding can be done with a wide range of plastic compounds, depending on your needs. At Aptyx, we’re material experts and have worked with just about every resin on the spectrum, including high-performance polymers such as PEEK, Ultem® and PSU and engineering polymers such as UHMWPE and HDPE. We can help you select the material that’s the best fit for your project based on cost, availability, and performance characteristics.
Plastic Injection Molding Advantages
Efficient high production
Once the mold has been fabricated, the injection molding process can manufacture parts quickly and reliably, making it an excellent choice for medium- and high-volume production.
Fast production
Our advanced quick-turn custom molding solutions, including our DME® Master Unit Die (MUD®) Quick-Change System, dramatically reduce mold changeover time, resulting in increased uptime and productivity and decreased tooling costs.
Molding multiple materials
Techniques like overmolding, two-shot molding, and in-mold decoration can provide a seamless bond of multiple materials into a single part or product, at less cost than a secondary process.
Injection Molding Resources
What cleanroom classification is required for medical device injection molding and assembly?
Read Blog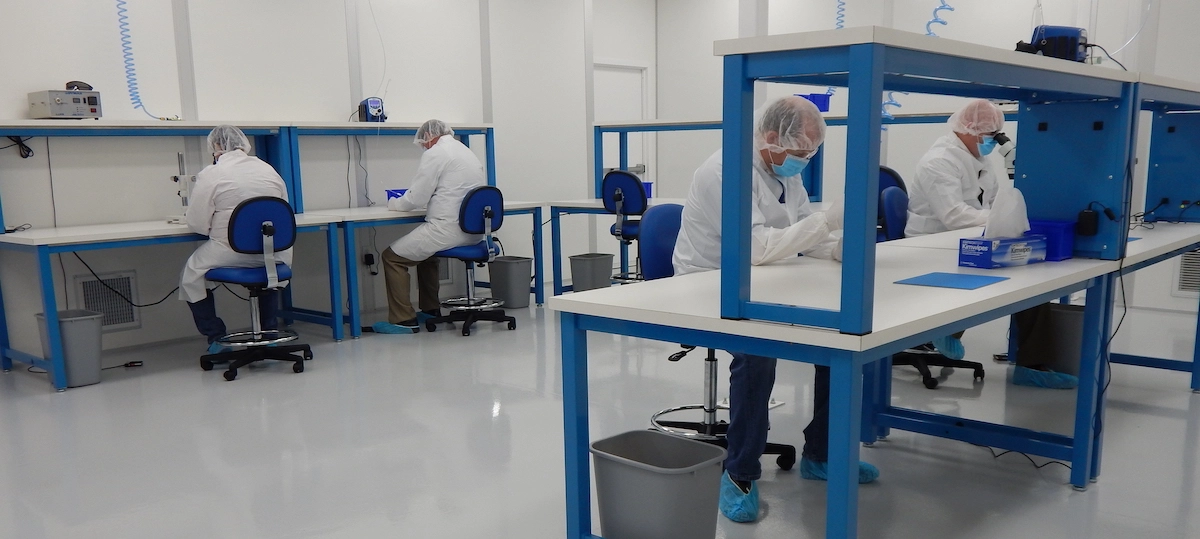
Capability Briefs
Precision gears, drivetrains & actuators: Driving mission-critical applications for over 70 years
Read Brief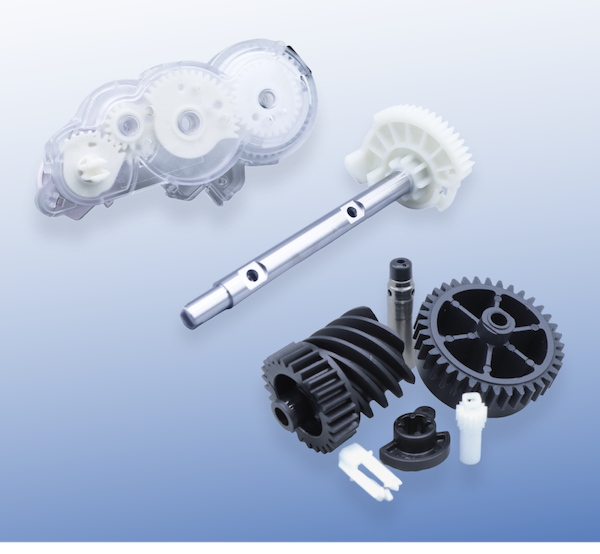