Industry-leading engineering solutions for your industrial manufacturing challenges.
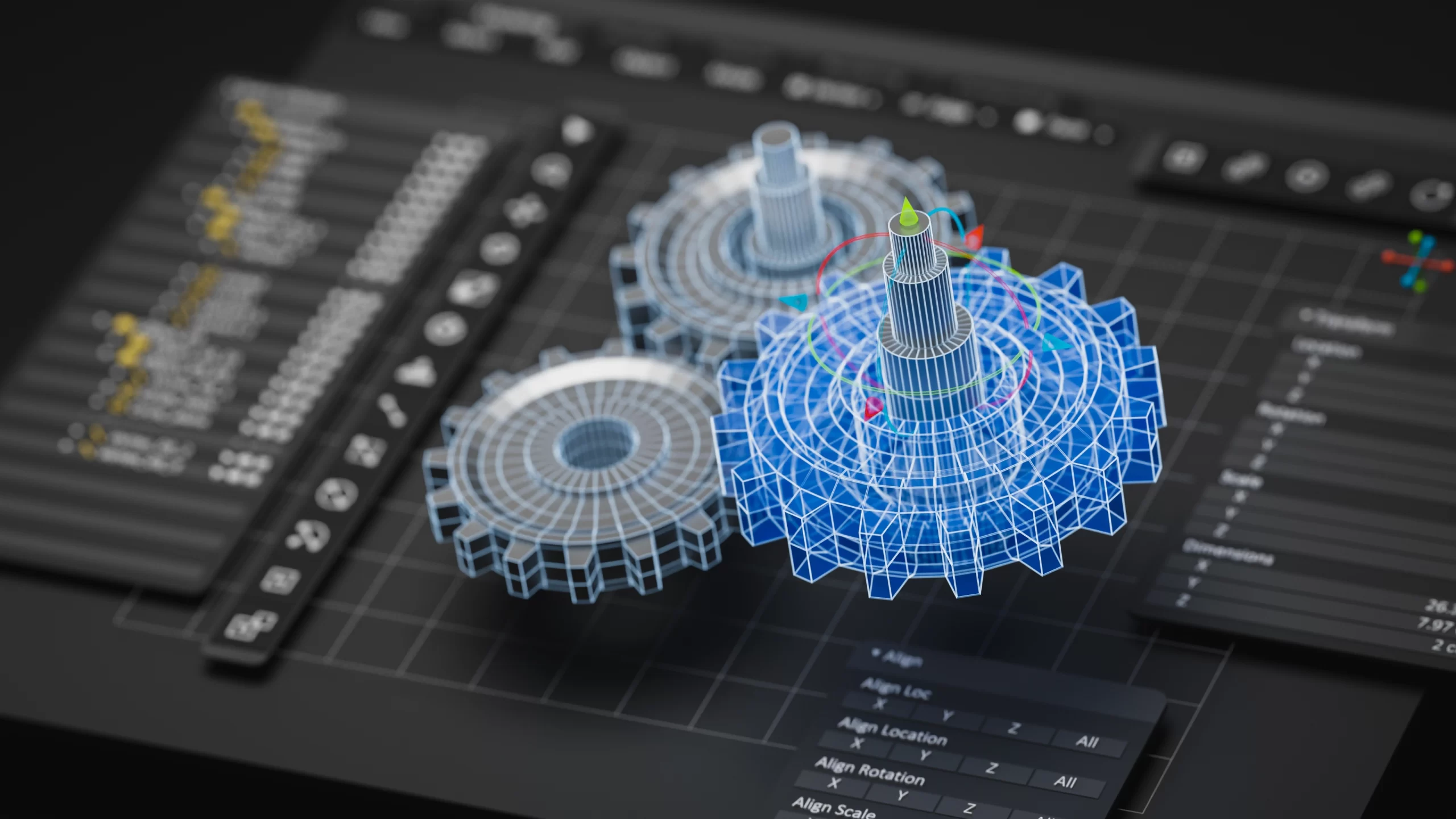
- Engineering minds, entrepreneurial spirit – Our engineers have pioneered breakthrough solutions to raise performance and solve complex challenges.
- Dedicated partnership – Expert engineers take ownership of every project, ensuring alignment with the customer’s vision and a smooth transition from start to finish.
- Local expertise, global reach – Our engineering teams collaborate across facilities to deliver smart, effective solutions that work for your unique needs.
Expert project management to ensure alignment
Your dedicated Project Engineer will take ownership of your project from proposal through production, ensuring continuity and bringing institutional knowledge on the best design and manufacturing approach for your project. You also have a dedicated Project Manager as a single point of contact to ensure effective communication and a smooth transition from development to manufacturing.
- Estimating
- Project Award
- Component DFX
- Tool Design
- Tool Build
- Process Development
- Qualification
Customized engineering services for complex manufacturing.
It’s one thing to create a beautiful design, but another to engineer that design for production. We take a proactive approach to every project. Our team of world-class engineers will collaborate with you on your vision for the project and review the design to identify opportunities for optimization. An engineering review may include an analysis of the manufacturability of the design, mold flow analysis, tool design analysis, and more. Our engineers and craftspeople leverage cutting-edge tools and technologies to provide a range of engineering services to optimize both tool and part design to ensure manufacturing success.
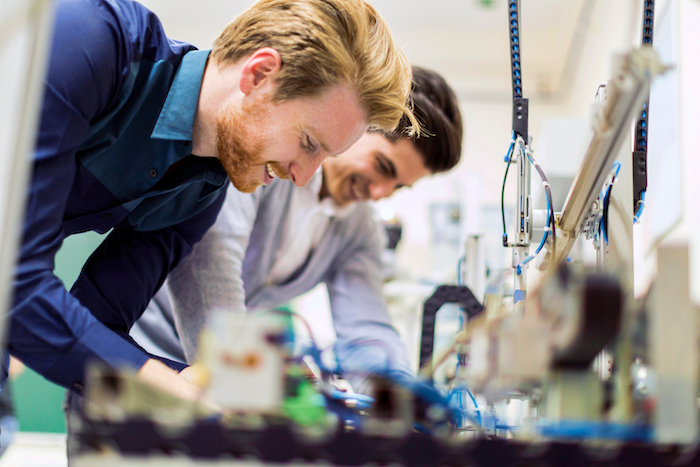
Design Support & Engineering
Our experienced team of engineers will review your new product concept or your existing device using design for manufacturability (DFM) and finite element analyses (FEA) to uncover ways to optimize your design to enhance manufacturing efficiency. Predictive engineering tools such as Moldflow® simulation reveal how resin will fill a mold during the injection molding process. These tools help us to understand the critical specifications of your components so that we can optimize mold design, improve mold efficiency and cost competitiveness, and reduce lead time.
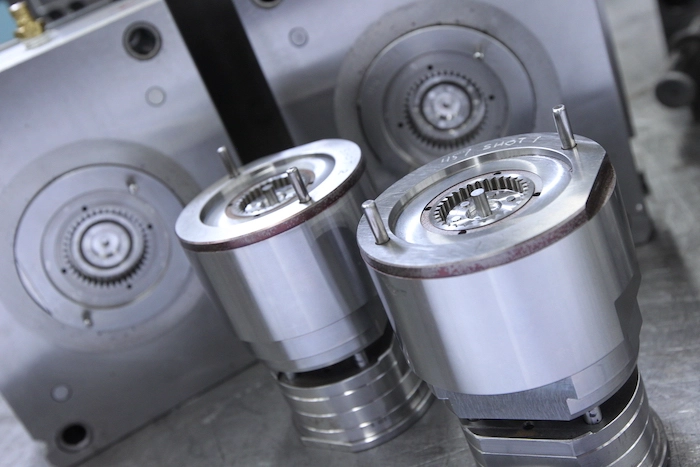
Tooling Design & Fabrication
A high-quality, precision-manufactured, well-maintained tool or die is the first step of a successful customized molding solution. Our team of experts includes tool makers and RJG Master Molder®-qualified engineers and technicians with decades of experience. We provide a full suite of tooling services to ensure your project’s success, including in-house custom tooling design, a range of tool-building capabilities in several geographies, tooling support services, and in-house tooling maintenance. Our Q-Drive Mold System is ideal for quick-turn injection molding of small plastic parts, including complex applications such as gears.
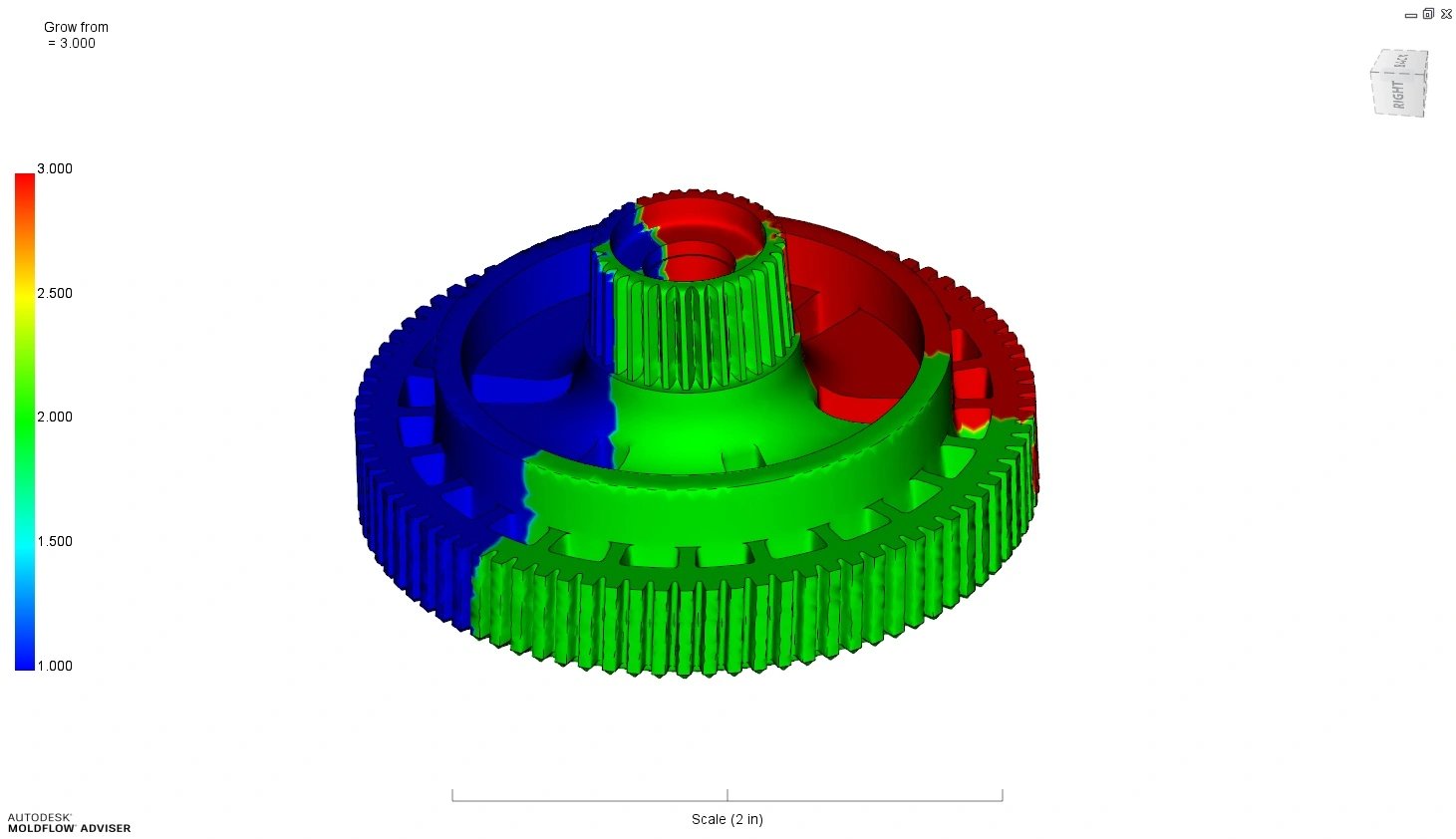
Engineering Services
Aptyx offers a full suite of engineering services, including:
- Scientific qualification with RJG Master Molder®-qualified engineers
- IQ/OQ/PQ full capability studies
- Mechanism development
- Complex CAD surface modeling
- Design for manufacturing to ensure tooling-ready injection molded parts
- Materials and process technologies
- Design for assembly and cost reduction
- Modular tooling systems
- In-house tool design
- Complete tool build capabilities
Your industrial partners in engineering and manufacturing success.
Quick-turn tooling
With our quick-turn Q-Drive program, we can design and build a tool in 2-4 weeks. Our state-of-the-art DME® Master Unit Die (MUD) Quick-Change System combines a static frame with interchangeable companion insert molds, dramatically reducing changeover time. The result is increased uptime and productivity and decreased tooling costs.
Predictive engineering
We’ve made a significant investment in predictive engineering and Moldflow® simulation and analysis. These tools help us to understand the stress areas, tolerances, and mating components of your parts, enabling us to work with you to optimize your design and build a tool that will reliably manufacture high-quality complex products.
Materials expertise
We can recommend the best material for your manufacturing process, potentially saving costs while enhancing performance. We have decades of experience in high-performance polymers such as PEEK, Ultem® and PSU, engineering polymers such as UHMWPE and HDPE, as well as commodity polymers. We also work with filled materials utilizing fillers such as BaSO4, talc, carbon, and glass.
Manufacturing smart
solutions for critical markets.
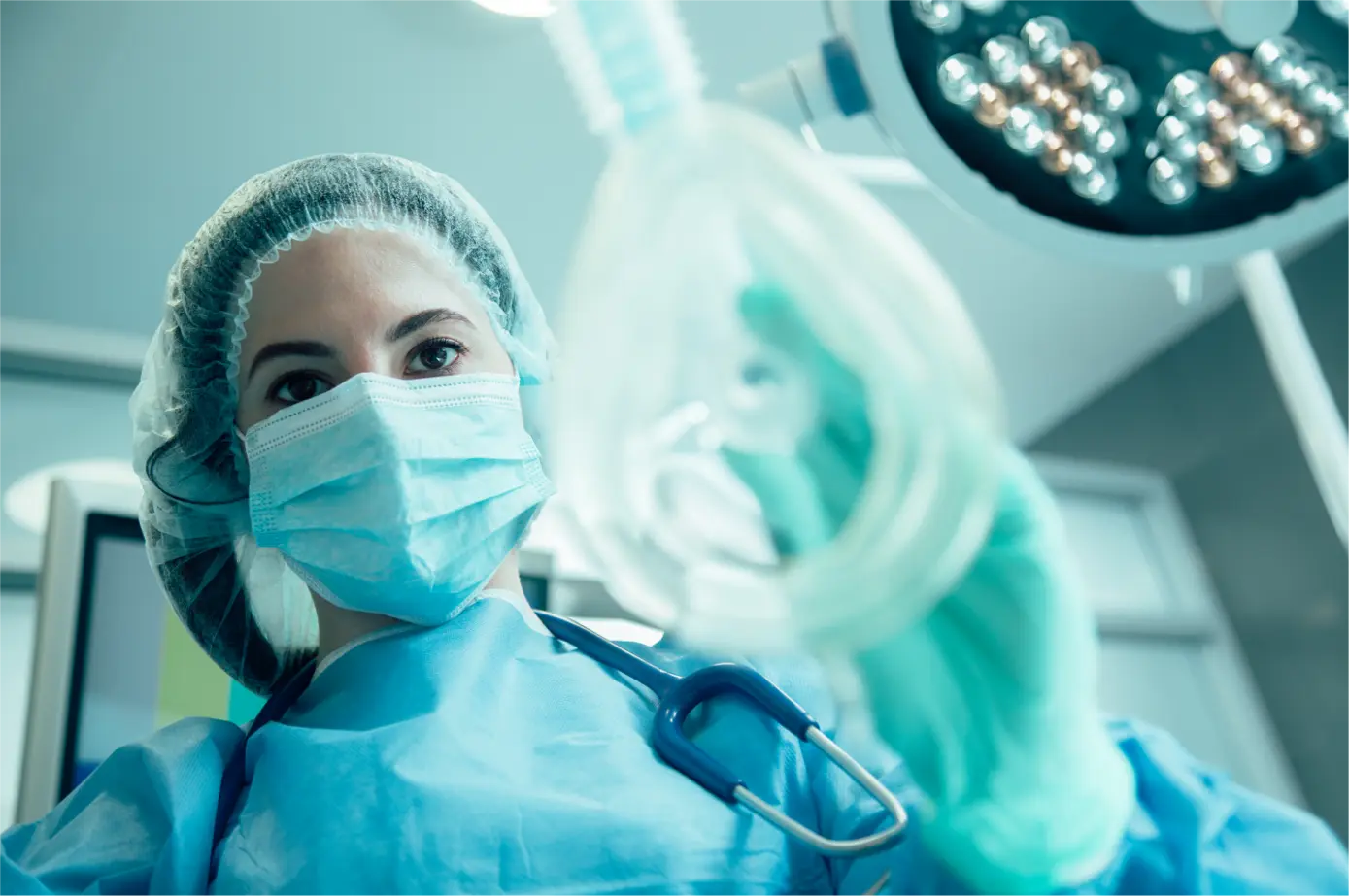
Medical Devices & Life Sciences
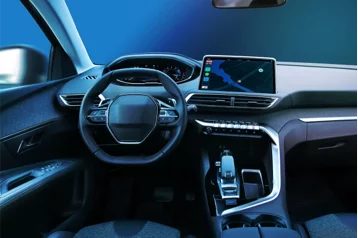
Industrial
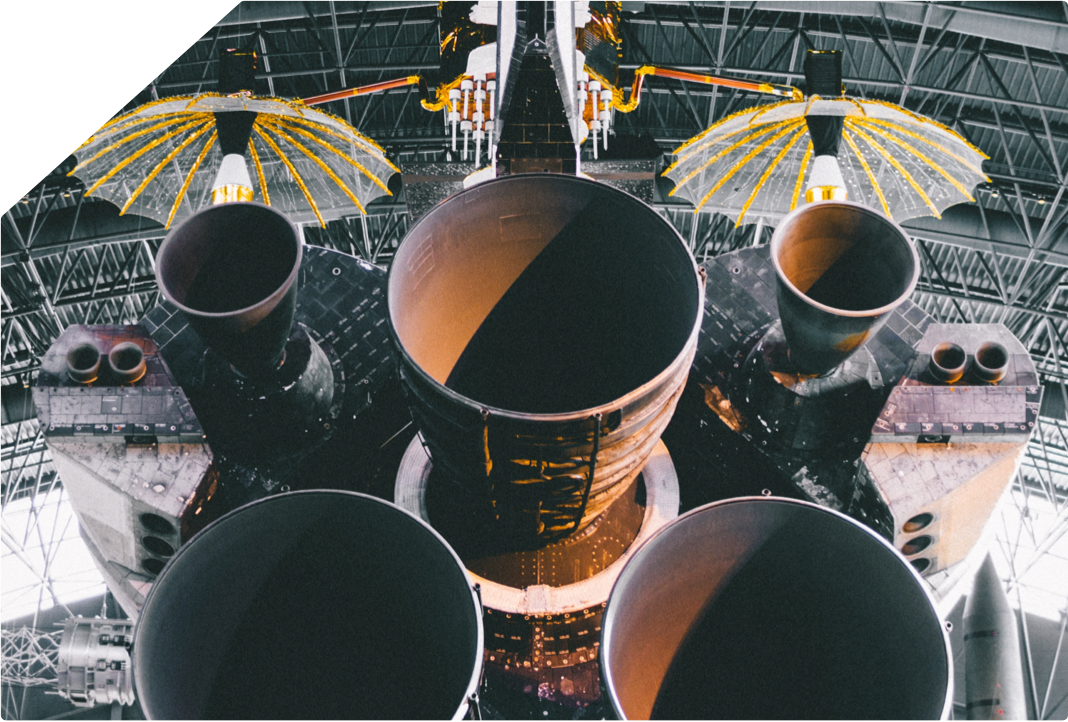
Aerospace & defense
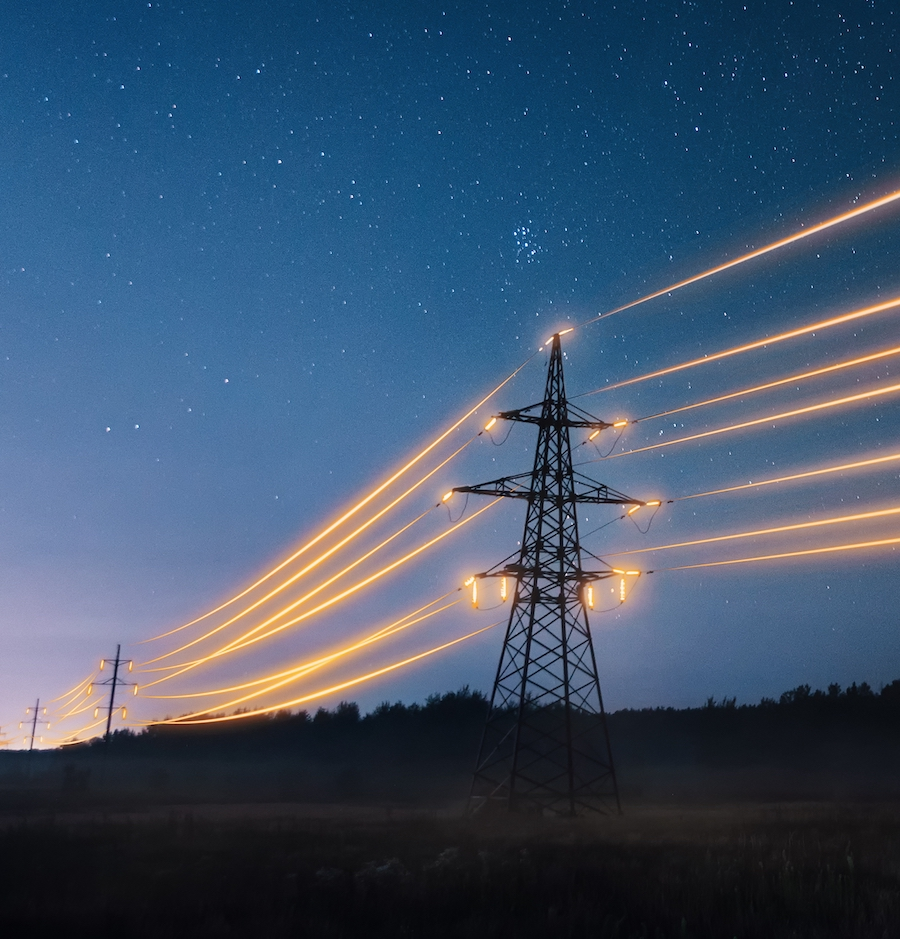
Energy
Engineering Resources
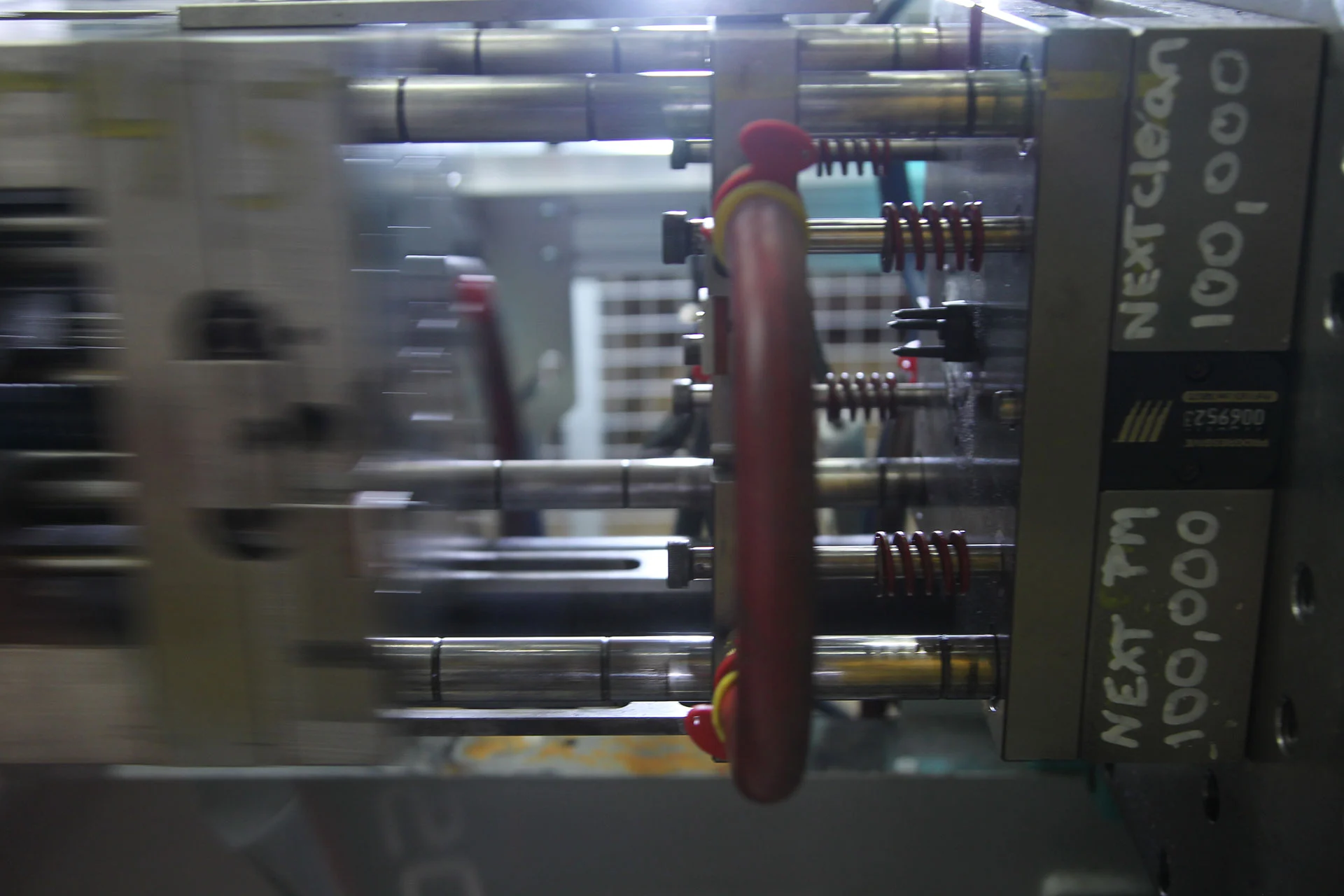
24/7 access to case studies, blog posts, capability briefs and other helpful information
Explore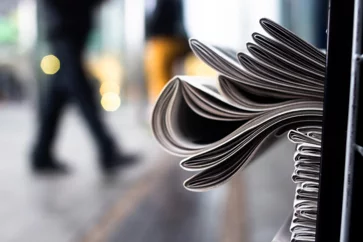