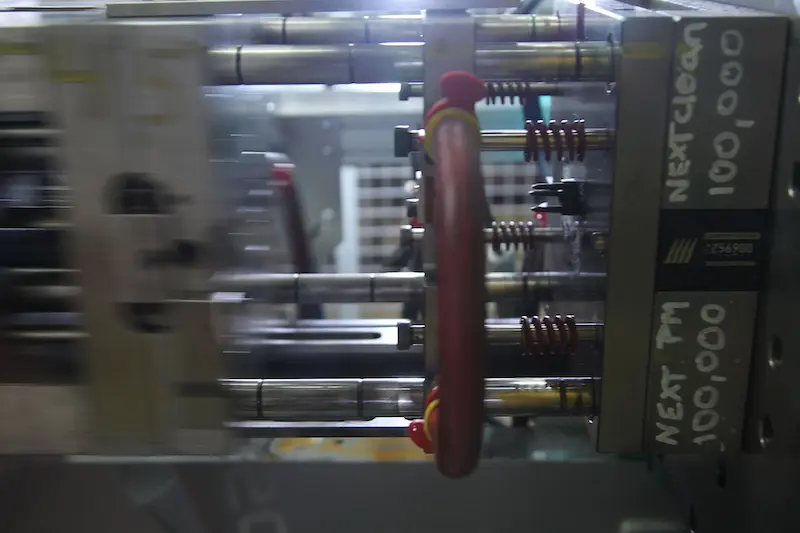
Both hot and cold runner systems are used in injection molding and the choice between the two is typically dependent on factors such as production volume, specifications and budgetary goals. Let’s start with a definition of the two types of systems and then dive deeper into each of the differences of a hot runner versus cold runner.
A hot runner system heats the molds and runner channels to keep material in a molten state for the duration of the injection process until it flows into the mold cavity, eliminating potential runner scrap.
In a cold runner system, the runners do not remain molten but become solidified plastic during the molding process and must be removed from the mold and plastic part after the molding process is completed.
Hot Runner Molds
Hot runner molds rely on manifold systems that become part of a mold. These systems are heated to the melt temperature of the resin. This allows parts to be direct gated without any form of scrap.
The hot runner systems utilize two primary gating methods. One method utilizes a hot tip, which is a continuous flow channel into the part that freezes off before the molding cycle is complete. It can leave a small gate remnant. Another method is the use of valve gates. Under this method the plastic flows through a hole that is sealed off with a pin. The aesthetic value is often much better than a hot tip. The valve gate is a common choice in the medical device industry as it promotes fast cycle times, reduced shear rates and improved gate aesthetics.
Hot runner mold systems are valued for their ability to produce consistent quality within faster cycle times. Although more expensive than cold runner systems in initial cost and ongoing maintenance, they don’t generate waste, thereby offering long-term savings potential.
Cold Runner Molds
Cold runners utilize flow channels cut into a mold surface. Molten plastic flows through these channels before entering part cavities. After the resin cures, both the part and the runner are ejected from the mold. Frequently the runner is automatically removed from the part as it ejects. Since cold runners degate using a shearing process, they often leave a small remnant on the part surface. The runner thickness must be larger than the part thickness to produce consistent quality. This usually causes cycle times to be longer than hot runners.
Cold runner mold systems are less expensive and easier to maintain than hot runners; however, they offer slower cycle times and create waste even if excess material is recyclable. As a result, cold runner mold systems typically have higher costs per part produced.
Are Cold Runners or Hot Runners Right for Your Project?
Both methods offer unique advantages, and can be utilized for producing a variety of different plastic parts and components. As with most systems, a key input in determining the right option are the needs of the business. For example, the importance of a lower upfront expenditure for the molds compared to the importance of the lowest cost per piece is a key input.
At Aptyx, our engineering team has decades of experience fabricating exceptionally well-made tools that produce quality parts. You can trust us to advise you on the best dip molding process for your project based on product design, performance requirements, and budgetary goals.