Gain a competitive edge with our dip molding solutions
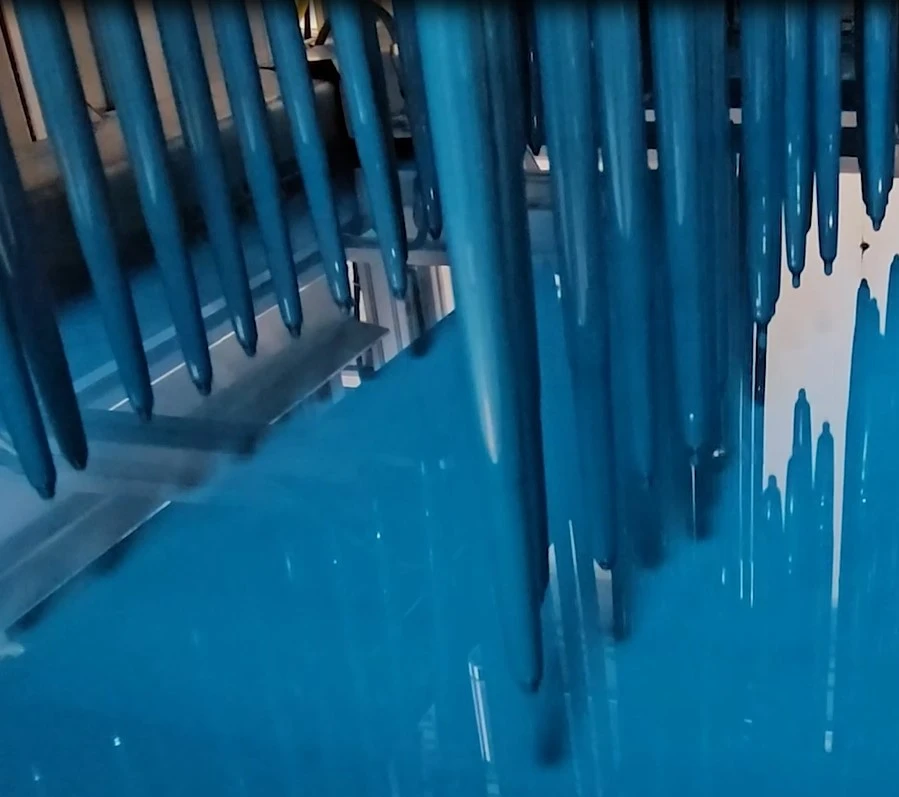
- Decades of leadership – With over 60 years of experience, we’re one of the largest and most versatile dip molding providers in North America.
- Trusted by OEMs – Customers count on us for high-performance dip molding and coating solutions for critical, high-spec applications.
- Advanced, automated systems – Our proprietary equipment includes continuous-motion and robotic batch systems built for your exact product and volume needs.
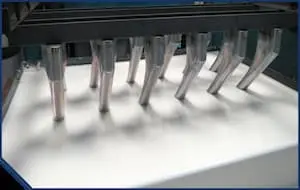
Contract Manufacturing
60-year legacy as a leader in manufacturing a diverse range of dip molded products and components.
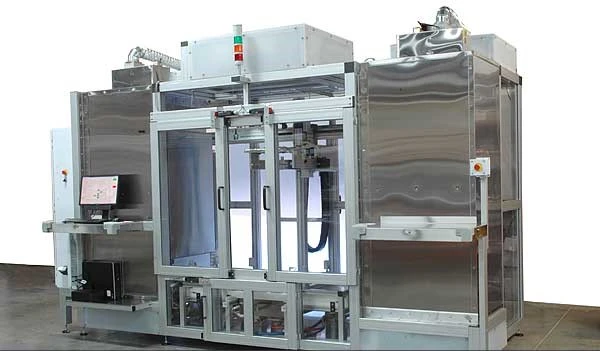
Dip Molding Equipment
Our experienced dip molding team offers concept design to full scale production equipment.
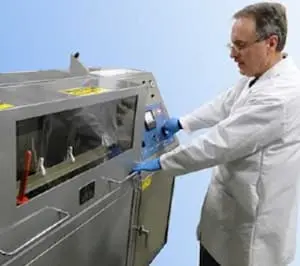
Product Development
Our knowledgeable technical staff can support the development of your dip molding project.
Expert dip molding for a wide range of materials.
Dip molding is the process of dipping a mold into a polymer solution to create a molded component. Our most commonly used dip molding material is plastisol (a suspension of PVC particles in a plasticizer) because it is a well-proven and cost effective material. When heated, plastisol fuses and is converted into a tough, homogeneous material with excellent resistance to abrasion, aging, corrosion, and electrical resistance. It can be compounded in almost any hardness, clarity, and color, and can be pumped or sprayed. With decades of materials expertise, we can work with you to identify the best material for your dip molding project.
Materials we commonly work with include:
- Plastisol/PVC
- Latex
- Nitrile
- Silicone
- Neoprene
- Polyisoprene
- Polyurethane
- TPEs
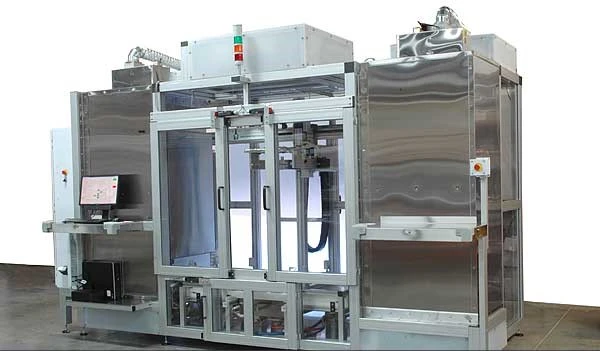
Advanced dip molding & coating equipment for demanding applications.
In addition to dip molding and coating services, Aptyx is the leader in the design and manufacture of innovative, highly reliable plastic dip molding and dip coating equipment for mission-critical applications. We offer technical services including mechanical and electrical design, project management, site installation supervision, and technical project business plan development. Our proven equipment designs help us to design a customized process to meet your production requirements with reduced delivery and start-up timelines. With decades of unmatched experience, we support a wide range of industries including medical, electronics, industrial, automotive, energy, agriculture and more.
Plastic Dip Molded Products
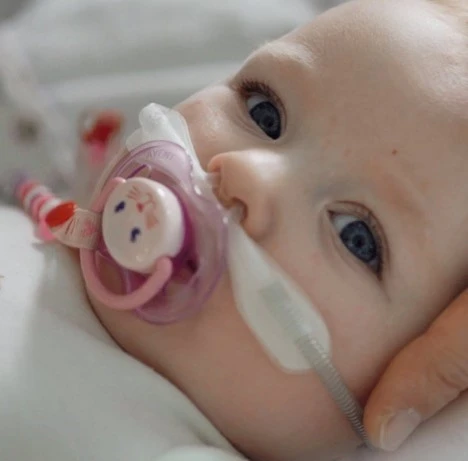
Nasal cannulae
Dip molding allows us to create complex geometries in a single component.
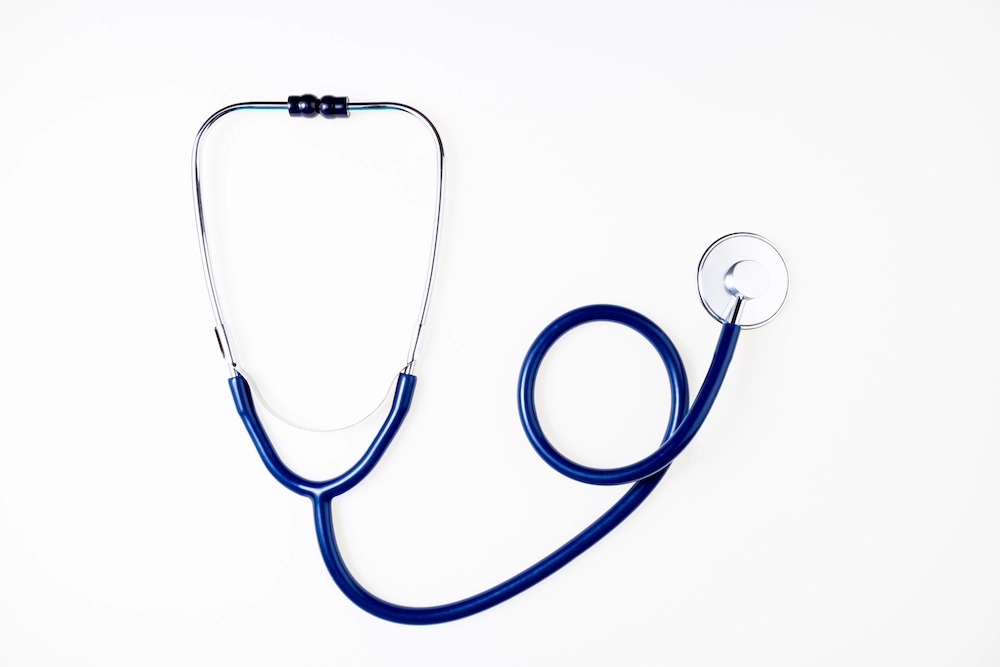
Stethoscope tubing
We dip mold stethoscope tubing in a wide range of colors.
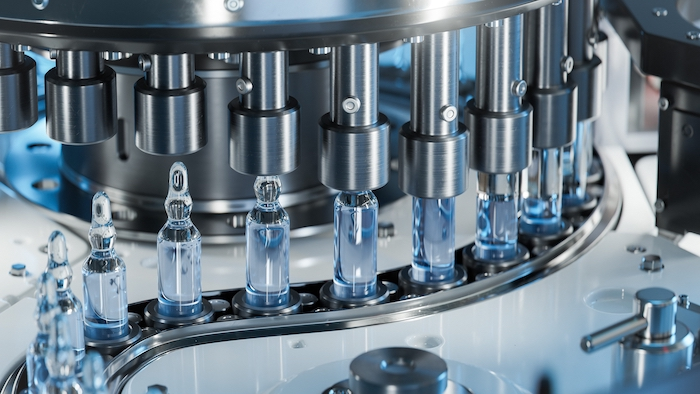
Spring-reinforced cannulae
We add spring reinforcement to dip-molded arterial and esophageal cannulae to maintain flexibility and prevent crushing.
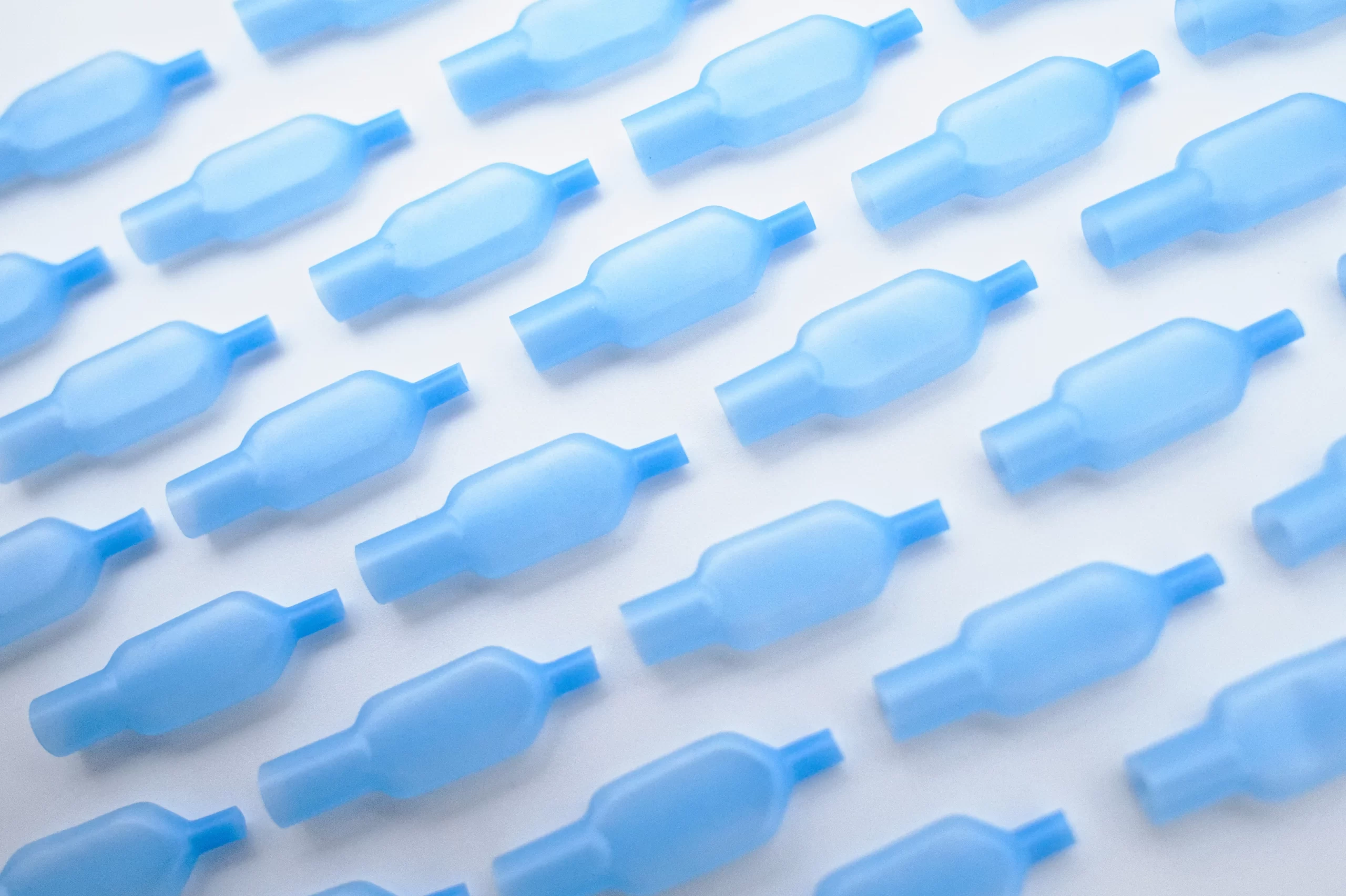
We dip mold medical balloons and cuffs for a wide range of applications including stent delivery, endoscopy, and urology applications.
Dip Molding Advantages
Rapid prototypes
Our manual dip molding cells are set up to accommodate rapid prototypes. Though tooling is necessary, tooling costs and lead times are much less compared with other molding processes.
Lower tooling costs
The tooling costs and lead times for dip molding tooling are substantially less than other custom polymer manufacturing processes.
Complex & elastic geometries
The dip molding process enables us to produce complex geometries more cost-effectively than with other plastic dip molding processes and it also enables elastic wall features.
Flexible process
Due to the flexibility of the dip molding process, it is easier to achieve a wall thickness that is much thinner or thicker than with other plastic manufacturing processes. It’s also easier to accommodate changes–such as adjusting wall thickness–after tooling is completed.