Implant innovation,
engineered for what's next.
END-TO-END IMPLANTS FROM CONCEPT TO COMMERCIALIZATION
"*" indicates required fields
- Design, development, and manufacturing of catheter delivery systems for the precise placement of critical medical implants
- Variety of applications including stent grafts, valve repair and replacement, occlusion, bioabsorbables, regenerative scaffolds, mesh, ureteral stents, nerve stimulation, gastric balloons, and infusion ports for drug delivery
- Tightly controlled cleanroom manufacturing and wealth of experience ensures repeatability of all products and processes
- Implanted material experience and material selection process, considering the entire lifecycle of a product
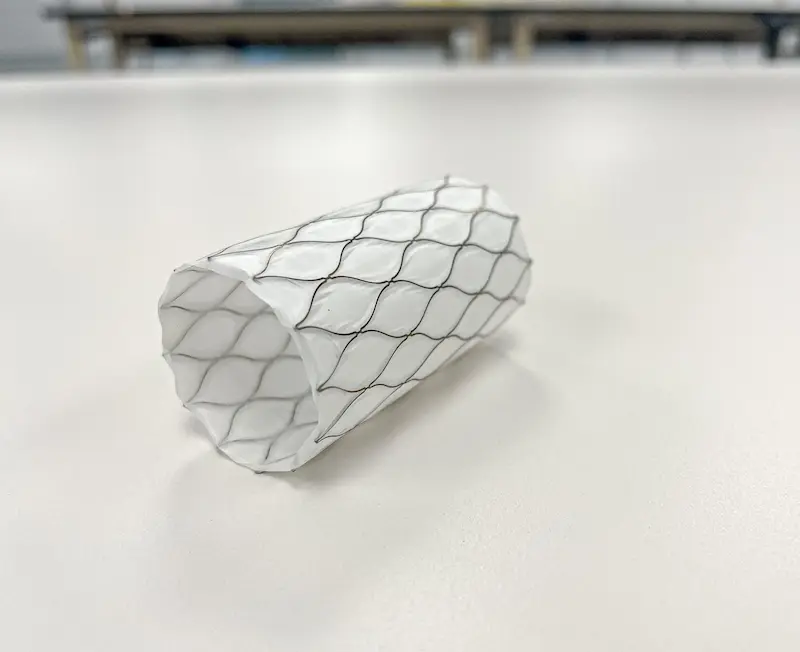
Our experienced engineers can assist you in developing covered stents and frames with unique shapes and profiles and wall thicknesses as low as 20 micron (0.0008″). Our expertise in sintering, sewing, laminating, dip casting, heat setting, and injection molding can help create the medical device prototype you need.
Clinical areas we serve include:
- Vascular
- Structural Heart
- Gastrointestinal
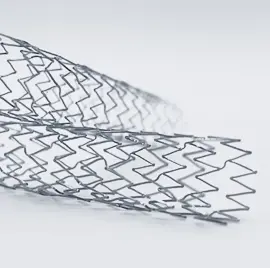
Aptyx has extensive experience in the design, development, and contract manufacturing of medical stents whether metallic or polymer based. We specialize in manufacturing medical devices intended to open narrowed tubes and vessels within the body to allow adequate flow of blood or fluid to pass.
In addition to stents, we also develop and manufacture medical stent delivery systems. Aptyx has experience with the following variety of stents:
- Stent Grafts
- Peripheral Vascular Stents
- Crossing Covered Stents
- Flow Diverters
- Ureteral & Urethral Stents
- Esophageal Stents
- Tracheal Stents
- Biliary Stents
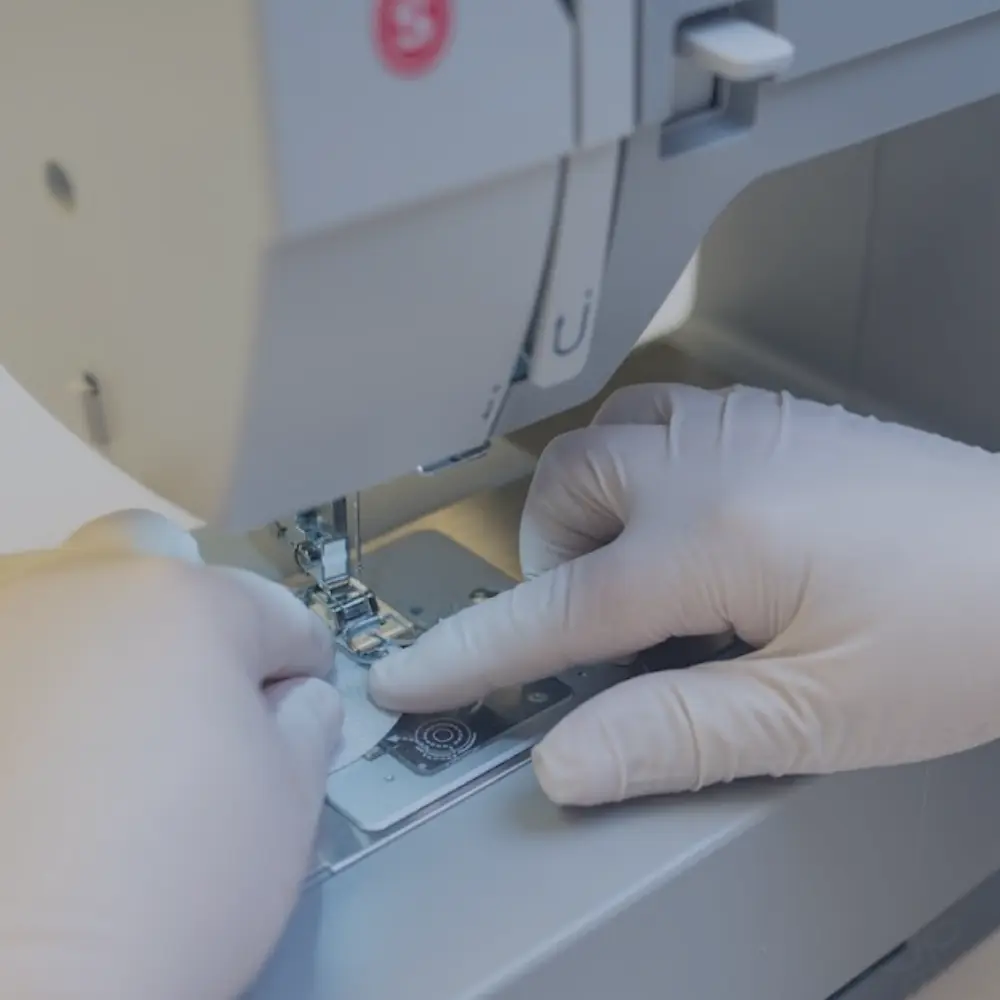
Aptyx continuously develops and manufactures innovative biomedical textiles and materials for cardiovascular, tissue engineering, and other surgical applications. Most biomedical materials used in the development or manufacturing process are found in:
- Braided Materials
- Knitted & Woven Materials
- Non-Woven Materials
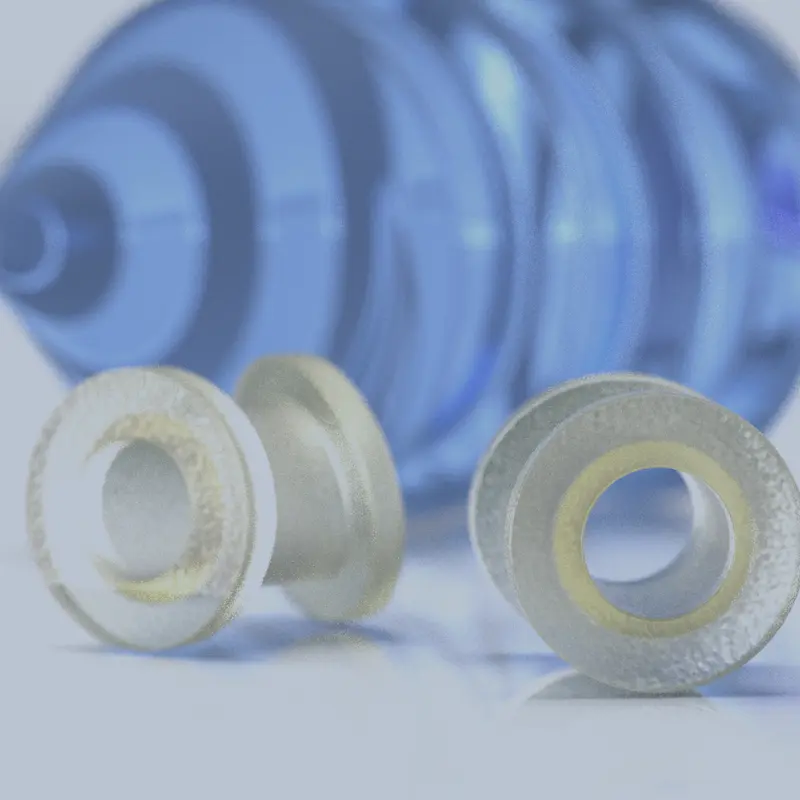
Using a bioabsorbable polymer in your medical device can allow surgical patients to heal without needing a second surgery to remove the device. These devices often lead to better surgical outcomes and lower treatment costs. Aptyx can tailor the composition of the specific bioabsorbable monomers or polymers for your device to meet specific requirements for absorption speed, tensile strength, stiffness, or toughness.
Some devices with bioabsorbable polymers we have developed & manufactured include:
- Vascular closure and repair devices
- Absorbable stents & braid, both components and subassemblies
- Fasteners, anchors, & screws and their delivery systems
- Tympanostomy tubes (Ear tubes)
Optimized material selection for advanced applications
Aptyx can support the design and material selection for your implanted device. When developing a medical implant, selecting the proper materials requires an understanding of the biological, physical, and chemical characteristics needed. Our material selection process considers the entire lifecycle of a product.
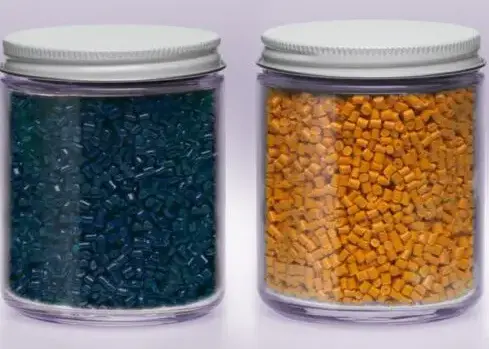
Material Selection Considerations
- Physical properties
- Biocompatibility
- Changes to material after implanted
- Willingness of supplier to sell raw materials for implanted use
- Processing limitations
- Cost
- Sterilization impact
- Shelf-life durability
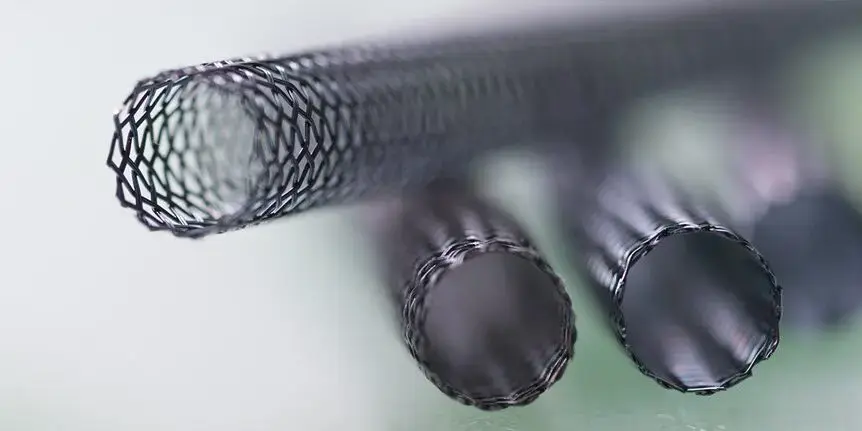
Our Implanted Material Experience
- PTFE and ePTFE
- Bioabsorbable / Absorbable
- Polyurethanes
- Liquid Crystalline Polymer (LCP)
- Polyester
- Silicone Rubber
- PEEK
- Polysulfone
- Nitinol
- Stainless Steel
- Other metals such as: Titanium, Cobalt-Chromium, Gold, Platinum, Platinum-Iridium
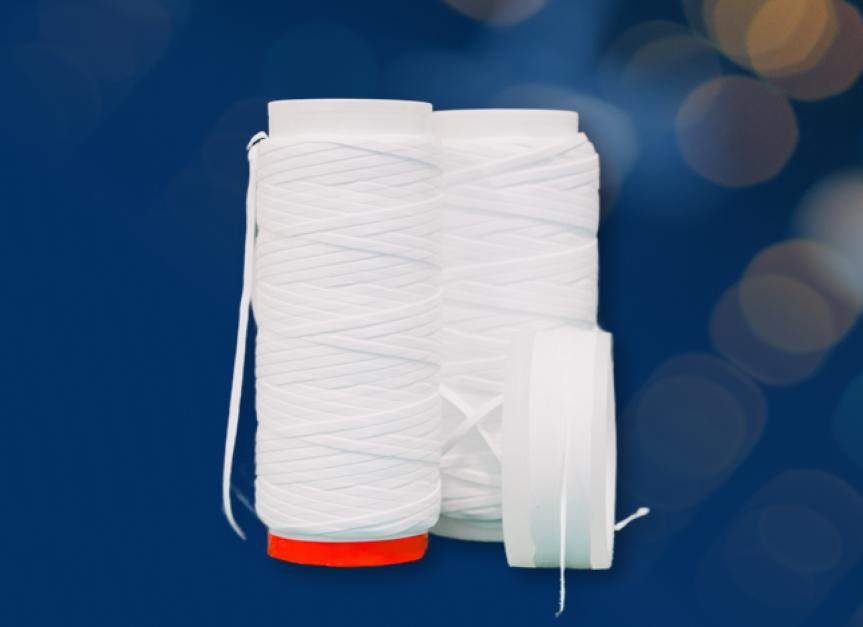
Learn about our breakthrough ePTFE solutions for implants and other advanced medical devices.
Read moreWe also provide testing of permanent implants to evaluate both design and performance standards. All testing is performed according to pre-approved protocol and conforms with required ISO and ASTM standards. Our testing supports regulatory filings, validations, and market comparison studies.
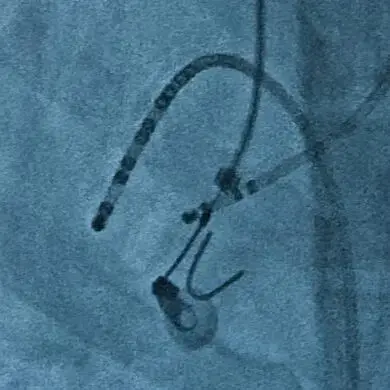
Examples of our medical device testing services include:
- Finite element analysis
- Mechanical properties
- Biocompatibility
- Corrosion testing
- Simulated use
- Radial force & crush testing
- Pulsatile durability
- Implant Deployment
- Degradation
- Radiopacity