Expert extrusion services for a
broad range of medical tubing.
Going the distance to provide customized extrusion solutions.
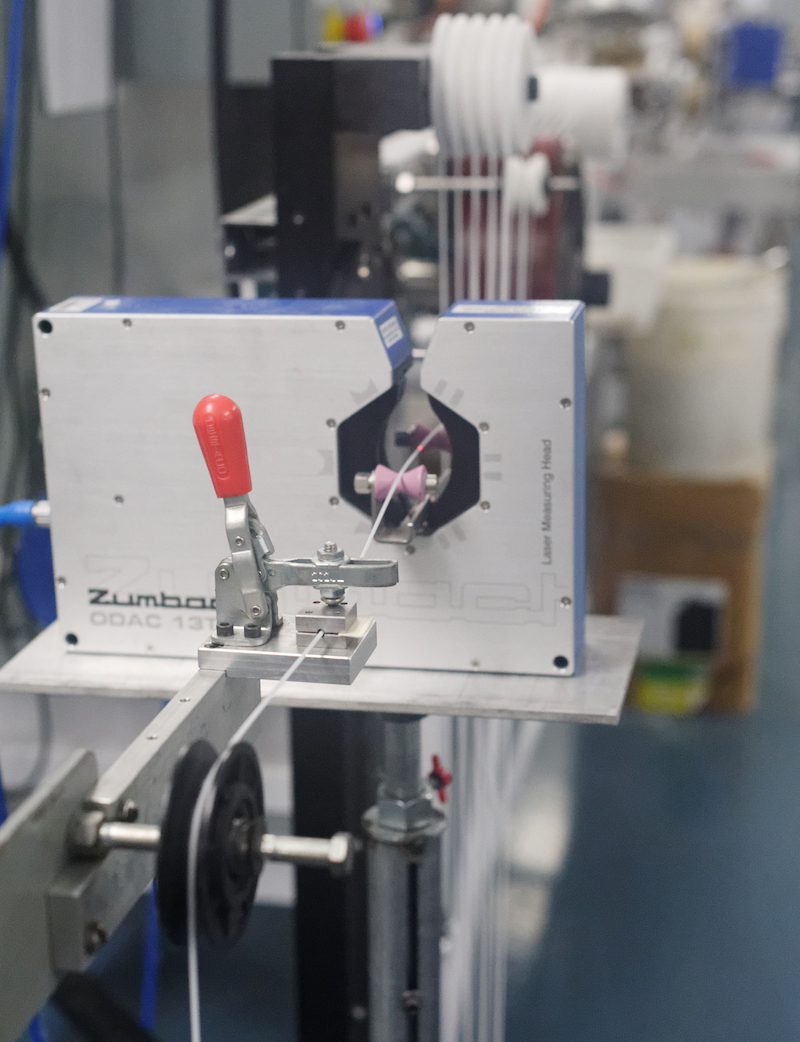
- Broad application expertise – We have more than 35 years of experience manufacturing a wide range of tubing for critical applications.
- High-volume capacity – We extrude millions of feet of tubing annually to support customers around the world.
- Customizable and complete – We partner with you to create custom medical tubing, with cleanroom assembly and value-add services available.
Advanced extrusion technology for complex profiles and shapes.
SINGLE- AND MULTI-LUMEN,
TAPER & PROFILE EXTRUSION
We extrude a broad spectrum of tube profiles to meet your needs, from single- and multi-lumen to taper and profile extrusions. Our custom extrusion capabilities include stripe, radiopaque, jacketed, and co-extruded products. We can extrude most thermoplastics, including polyurethanes, nylons, polycarbonates, PVCs, polypropylenes, polyethylenes, acetal, and custom-blended material.
Learn more
Core mandrels
Used as a manufacturing aid for braid- or coil-reinforced catheter and high-pressure contrast tubing, our precision-extruded core mandrels feature very tight tolerances to maintain consistent diameter, roundness, and a smooth surface during catheter extrusion processing operations. Materials include acetal and an acetal/silicone blend.
Learn more
Standard corrugated tubing
Aptyx is a leading manufacturer of extruded plastic corrugated tubing. We extrude EVA, PE and PP, as well as custom materials. Combined with our injection-molded plastic fittings, we offer a complete OEM product line of noninvasive disposable and reusable medical tubing and components for use in anesthesia, respiratory, and other medical and custom applications.
Learn more
Smooth corrugated tubing
Our smooth corrugated tubing is manufactured with a smooth interior to promote optimal air and gas flow for applications including sleep apnea, smoke evacuation, anesthesia, and respiratory tubing. Materials include EVA, metallocene, and Hytrel®.
Learn more
Expandable tubing
With one of the widest size ranges of expandable tubing on the market, we offer a complete OEM product line of non-invasive disposable medical tubing and components for use in anesthesia, respiratory, and other medical and custom applications.
Learn moreOur heated wire tubes are manufactured with a patented process to embed wire within a hose constructed with a series of helixes. You can create a custom configuration by choosing the shape and number of helixes as well as the number, position, and diameter of wires within the helix.
Learn more
Technology advancements that drive better performance.
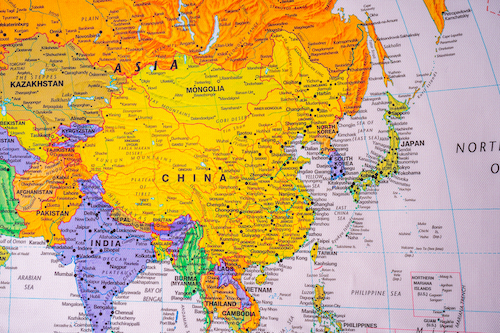
Extruded tubing that goes the extra mile. And then some.
Extruded Products
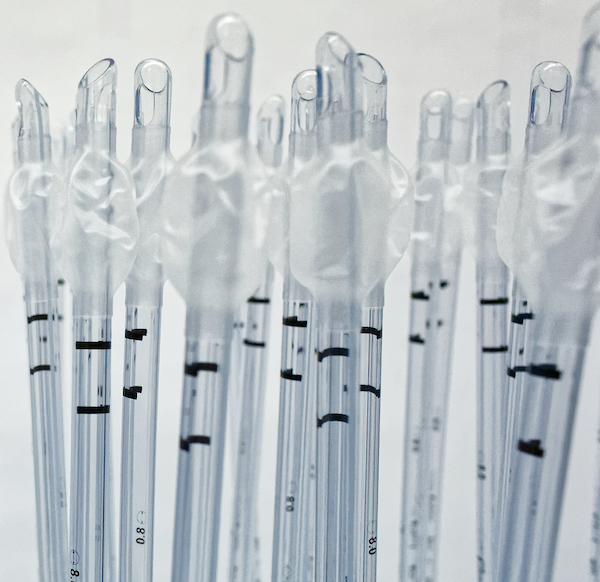
Endotracheal tubes
Often extruded as multi-lumen tubes, our endotracheal tubes can be co-extruded with a radiopaque line that allows medical professionals to visualize the tube under X-ray.
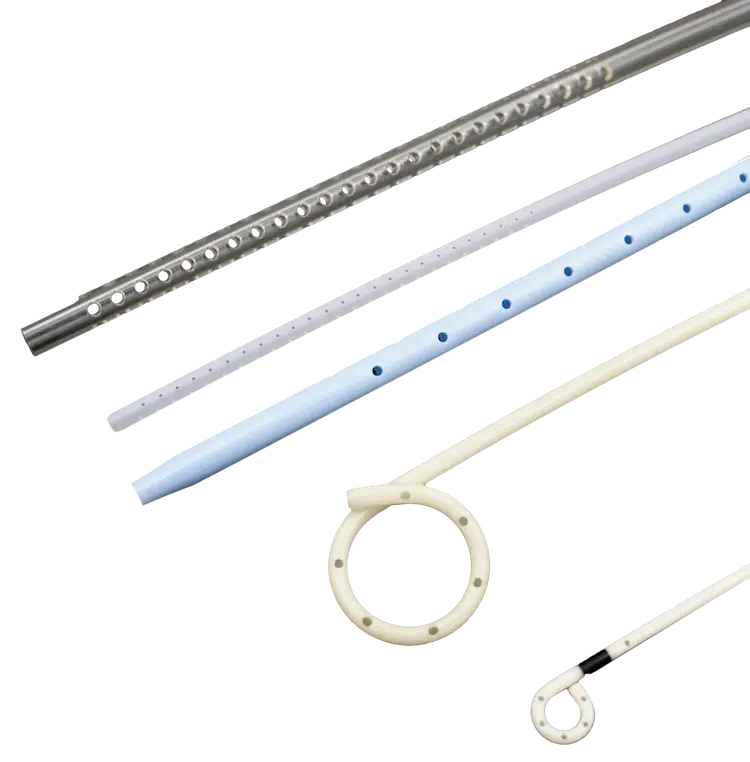
Catheters
We extrude catheters with complex features to meet performance requirements. We also provide cleanroom assembly to build complete catheter-based devices.
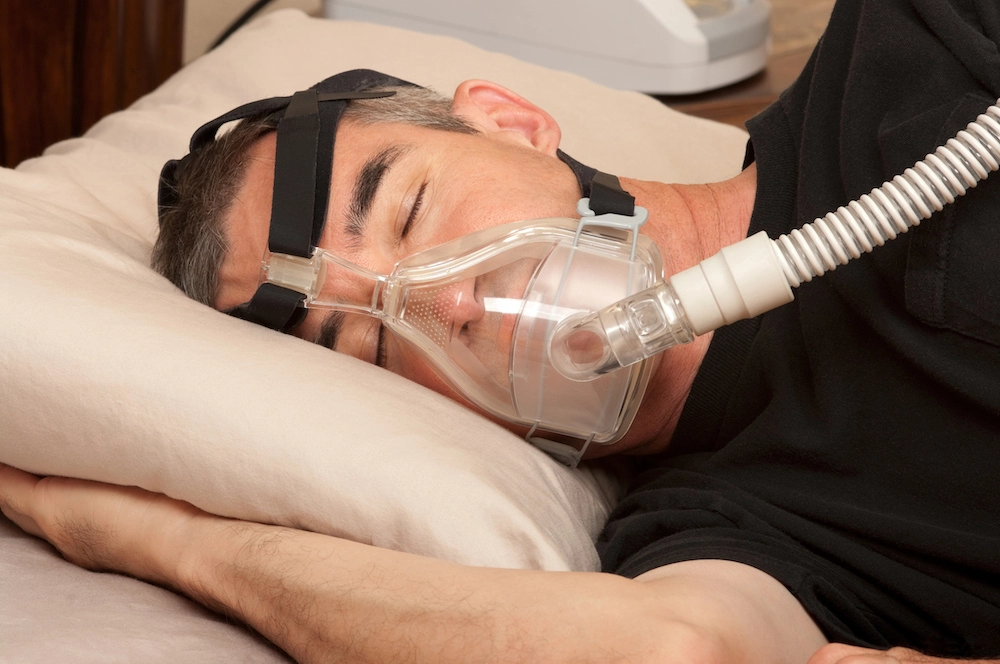
CPAP machine tubing
Our co-extruded polypropylene smooth corrugated medical tubing is used with CPAP machines to treat sleep apnea.
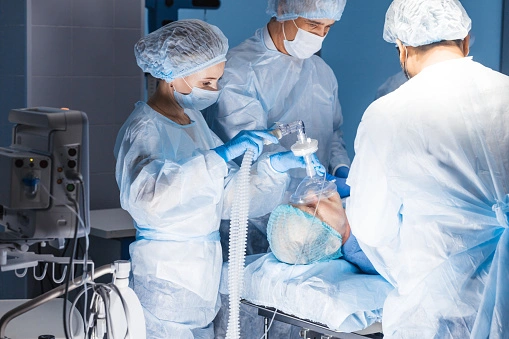
Anesthesia and respiratory tubing
We offer a complete product line of disposable and reusable medical tubing and components for anesthesia, respiratory, and other medical and custom applications.
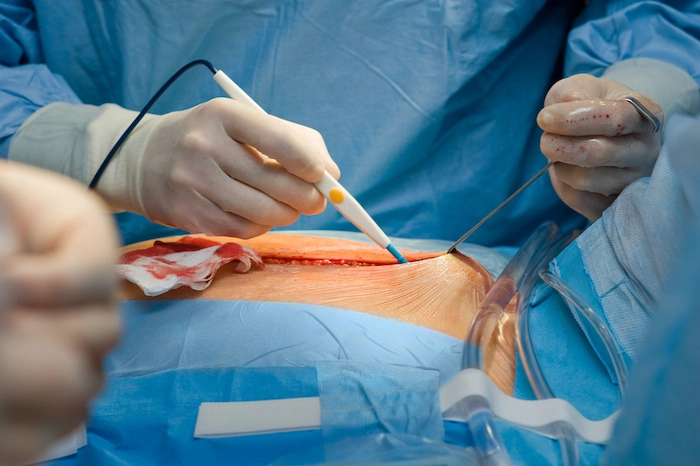
Surgical smoke evacuation tubing
We manufacture 40 million feet of smoke evacuation annually. This
smooth-interior EVA tubing promotes optimum removal of smoke from the surgical suite.
Extrusion Advantages
Complex geometries
The extrusion process allows for more complex geometries than would be possible with molding techniques; for example, multi-lumen and co-extruded tubing.
Sustainable
In the extrusion process most materials that are used can be recycled, minimizing waste.
Productivity
Medical extrusion lines can run continuously, allowing manufacturing facilities to operate 24 hours a day with multiple shifts, maximizing productivity.
Plastic Extrusion Services for Your Business
How custom plastic extrusion services are utilized by a wide range of companies
To recognize the true benefits of these plastic extrusion solutions, you’ll first need to understand the intensive chemical and engineering steps that help to create a reliable final product. This begins with sourcing the different raw materials that are necessary to form your intended type of plastic, which usually come in the form of granules, pellets, or powder that are loaded into a hopper to undergo the melting process.
As the material is led through a barrel, the screw within pushes the melted plastic forward and continues to mix it while surrounding external heating devices are used to apply the perfect temperatures from a full 360º angle so that everything is melting evenly.
Each individual plastic component for a project will require a unique die to be designed to fit the necessary specifications for the product, and ultimately, this custom-shaped tool is what the melted plastic solution will be fed into. Because the extrusion process requires high-pressure implementation into the die, it’s able to eliminate any potential irregularities, such as air pockets or other deformities. From here, the extruded plastic undergoes a thorough cooling process, and then any further cutting, trimming, or shaping can be completed to meet your unique requirements.
Extrusion resources
Airway management and respiratory delivery: Because every breath matters
Read brief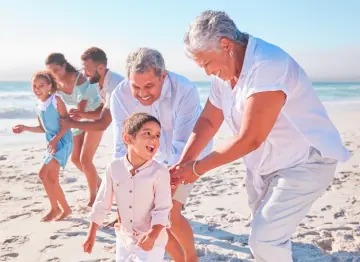
24/7 access to case studies, blog posts, capability briefs, and other useful information
Explore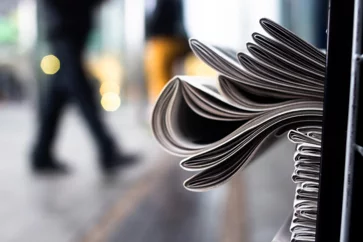