Q-Drive Mold System for your
quick-turn tooling needs.
FLEXIBILITY TO TAKE YOUR PROJECT FROM PROTOTYPE TO PRODUCTION.
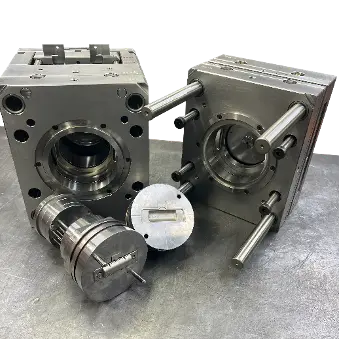
The Q-Drive Mold System comprises a custom tool insert that fits into a master Q-Drive mold base. It’s ideal for injection molding of small plastic parts, including complex applications such as gears. The customer owns only the custom tool insert, which saves time and cost. The flexible Q-Drive system can be used for prototypes, bridge tooling, and production.
Benefits
From prototype to production.
High quality
- Class 103 construction
- Hardened ground steel (54-56 HRC)
- Shot life: 250,000
Cost Savings
- Cost for tool insert only is a fraction of the cost of a full tool build
- Reduced setup time increases efficiency and reduces part cost
Flexibility
- Can be used as prototype tool, bridge tool or production tool (volume dependent)
- Suitable for validation and regulatory submissions
Speed to Market
- Building custom tool insert only saves time (typical insert build is 2-4 weeks)
- Design time and other process steps are also expedited
Specifications
Q-Drive Mold System
- Class 103 construction (54-56 HRC)
- Shot life: 250,000
- Capable of ±.003” tolerance (0.0762 mm)
- Compatible with broad range of thermoplastics
(not intended for Stanyl or TPU)
3.5" Insert
- Part shot size limited to 0.3 g
- Maximum part height: 1.125” (28.575 mm)
- Maximum part width: 2.500” (63.5 mm)
5.0" Insert
- Part shot size limited to 1.0 g
- Maximum part height: 1.500” (38.1 mm)
- Maximum part width: 3.000” (76.2 mm)
What our customers are saying
One particular capability where they really stand above competitors is project management. This is done in a professional way, and we have quite high complexity involved. They are doing an outstanding job.
Global Commodity Manager / Multi-national Medical Device Company
The Aptyx team did an excellent job converting brass gears to plastic. Because of the design challenges, deep expertise in gears and over-molding was crucial. They also converted an expensive, labor-intensive part with quality issues to two-shot molding, which dramatically reduced cost, improved quality, and easily met the production needs. Apytx came through for us because of very good program management and good technical expertise.
Lead Principal Engineer / Global Medical Device Company
Working with your team has been one of the best contract manufacturing interactions ever. They made the whole thing happen even when it was chaos on our end.
Director of Regulatory Affairs/Product Development Manager / Medical Device Startup
What we do matters. Working with teams of experts from across our global network, we’re able to combine skillsets and knowledge to provide the best products and services for our customers. At Aptyx, learning is valued and we have opportunities to pursue courses and training that support our professional aspirations.
Janet M. / Program Manager / Torrington, CT facility
Download the Q-Drive Spec Sheet