Specialty coating application and
equipment for advanced performance.
End-to-end coatings support, from application to automation.
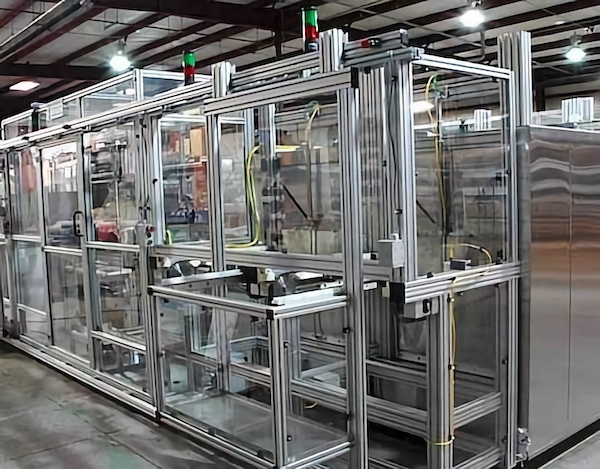
- Full-service solutions – We support you from identifying the right coating to designing, building, and installing application equipment.
- Leaders in automation – With decades of unmatched experience, we lead in automated systems for the application of a wide range of dip and spray coatings.
- Diverse expertise – We have completed more than 500 projects in the last decade, and currently support customers in more than a dozen countries.
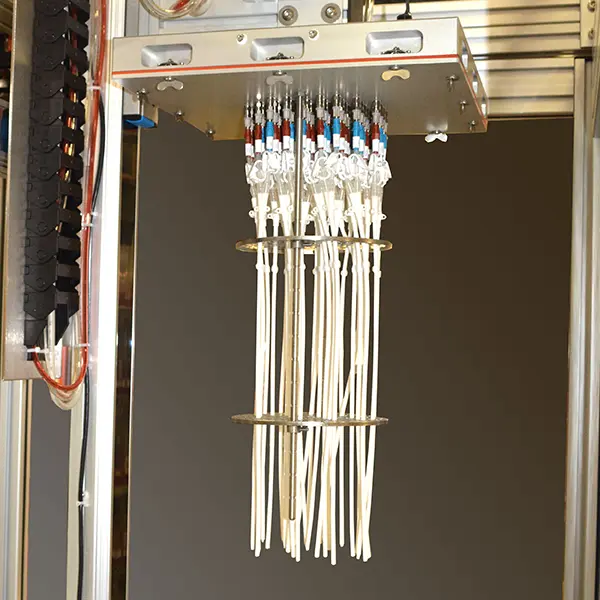
Dip Coating
End-to-end support from application to automation in partnership with leading coatings suppliers.
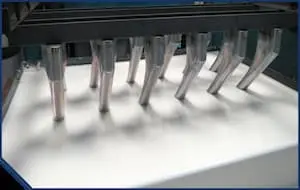
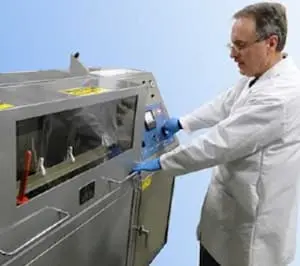
Full-Service Development
Our experienced technical staff can support the development of your dip coating or molding project.
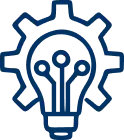
In the R&D phase, our experienced technical staff can help your company advance your dip molding or dip coating project by reviewing polymer options, tooling design, equipment requirements, and long-term production support needs. Our in-house laboratory service offers product and process development, as well as small-scale production for testing and marketing use. We can help with:
- Product Development
- Prototype Development
- Tooling Development
- Process Development
- Equipment Development
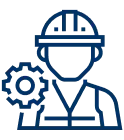
Our technical services include mechanical and electrical design, project management, site installation supervision, training, and technical project business plan development. Using the latest 3D CAD systems, our highly skilled engineers and designers can create comprehensive build packages for the most demanding coating equipment or product design specifications. Our engineering services include:
- Mechanical design
- Electrical hardware and software design
- Machine Design
- Conceptual design
- Plant and production flow layout
- Dip-molded product design & development
- FEA analysis
- Technical documentation packages
Coating equipment to meet every need.
We provide an extensive array of dip molding and dip coating equipment and related support equipment, such as pinhole testing, automated loading, and product removal or stripping systems. Our reliable, proven equipment designs allow us to achieve customized process and production requirements with reduced delivery and start-up timelines.
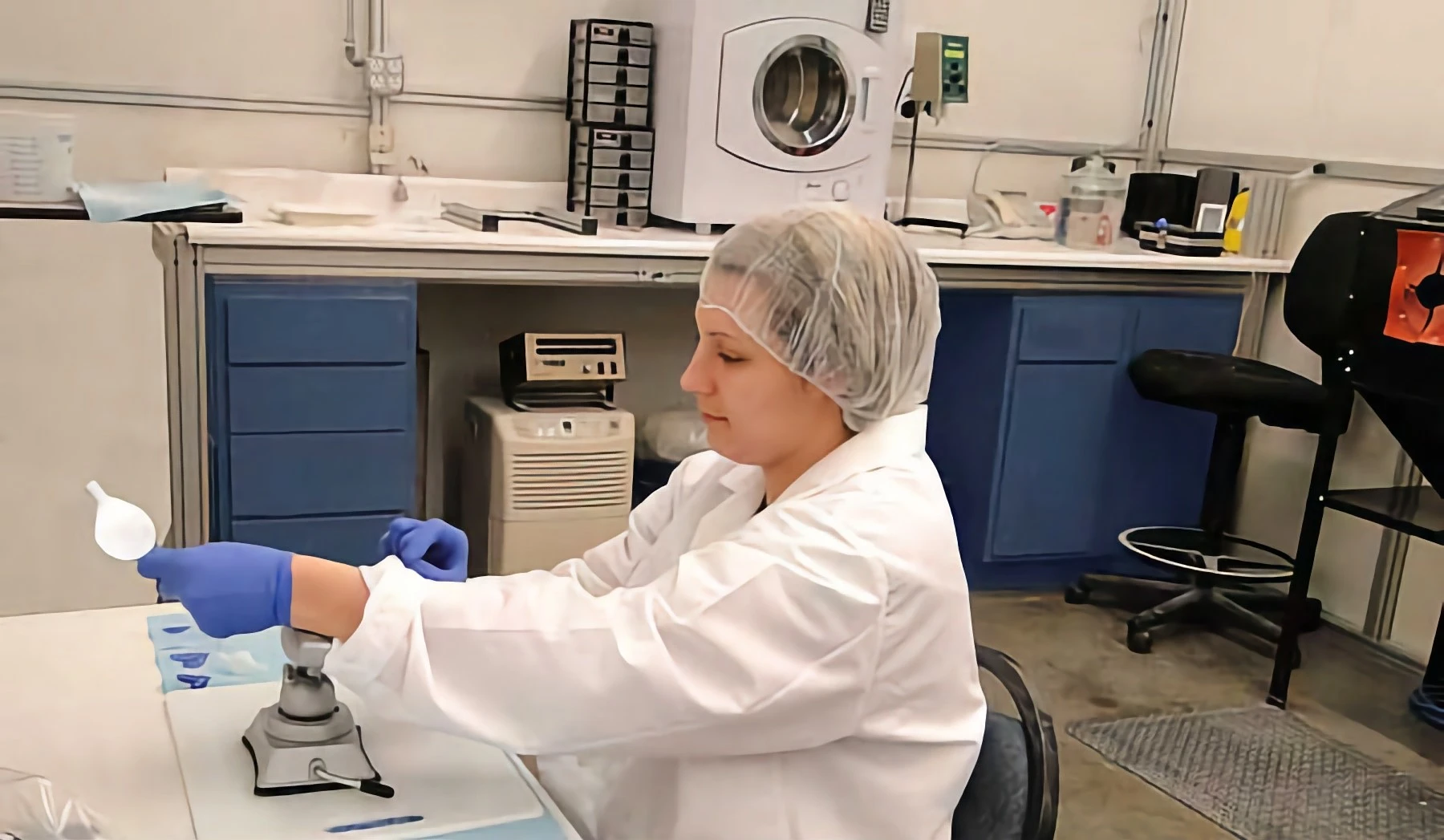
Research & Pilot Scale
Our Diplomat series laboratory and pilot equipment platform can help you with your R&D needs. It’s ideal for pilot and small-scale production requirements and can help you to evaluate multiple polymers or solutions and to define your process.
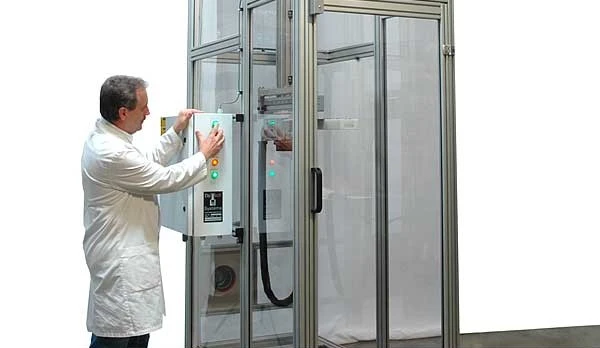
Production Equipment
Our team has the expertise to help you select the best size and type of equipment to optimize your project success. We also can help you validate your customized equipment, including installation qualification (IQ), operational qualification (OQ), and performance qualification (PQ). Production equipment options include:
- High-Volume Chain Line
High-volume continuous-chain dip coating systems, often referred to as drag chain lines, offer high-volume capacities for narrow product families with defined process parameters. These systems are capable of producing more than 1000 pieces per minute. - Batch
Batch or robotic-style equipment offers the ability to repeatedly perform complex manipulations for large arrays of product sizes, geometries, and polymers. These systems allow you to vary process parameters through the control system to accommodate chemistry and product changes.
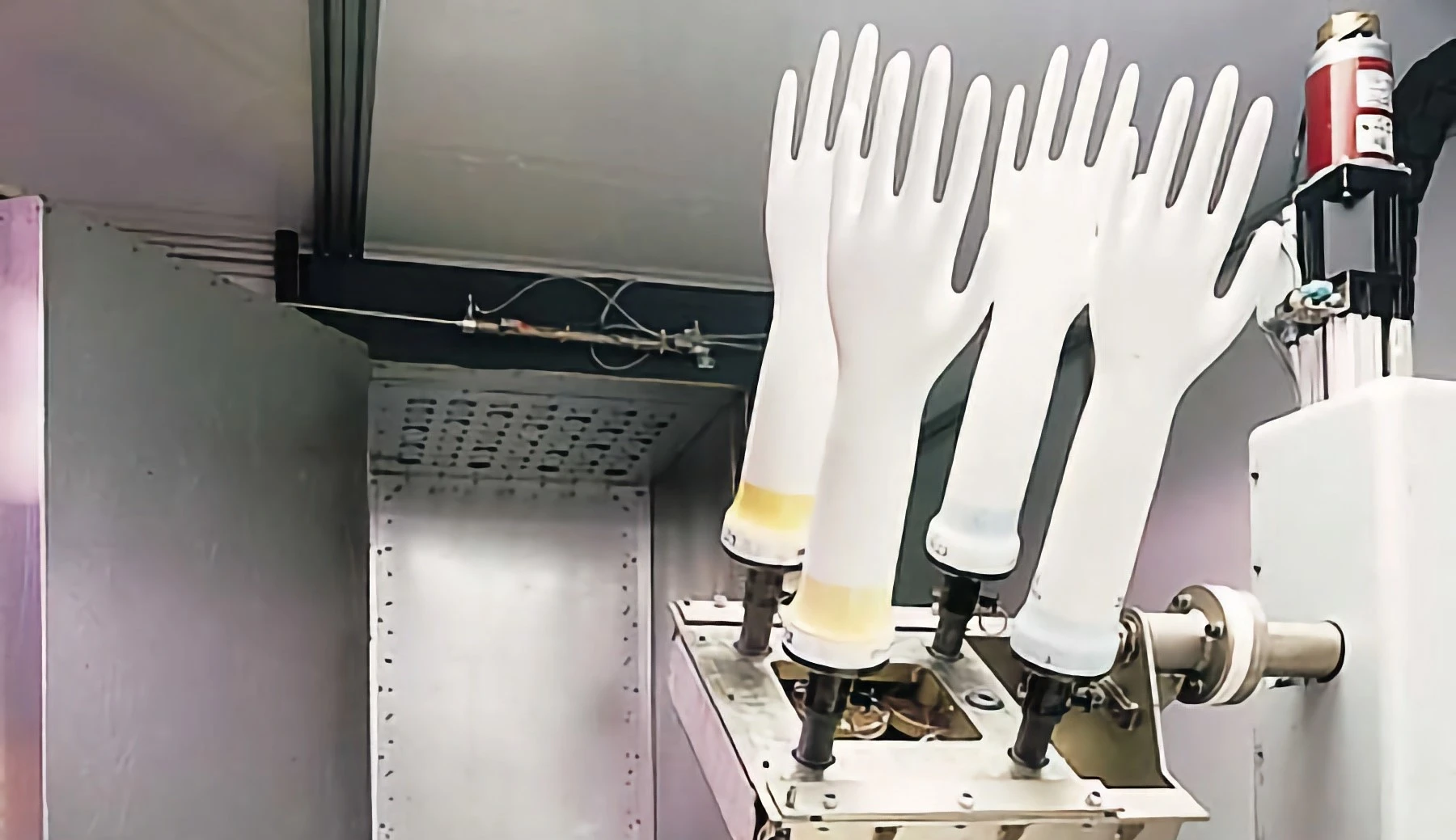
Test/Inspection Equipment
Thin-wall dip-molded products are often tested to detect functional imperfections in the film, called pinholes. For example, the FDA requires barrier integrity testing for medical exam gloves.
We offer testing equipment for all test methods, including:
- Glove water leak test stands
- Condom water leak test stands
- Condom conductivity test systems
- Glove inflation test systems
- Bag inflation test systems
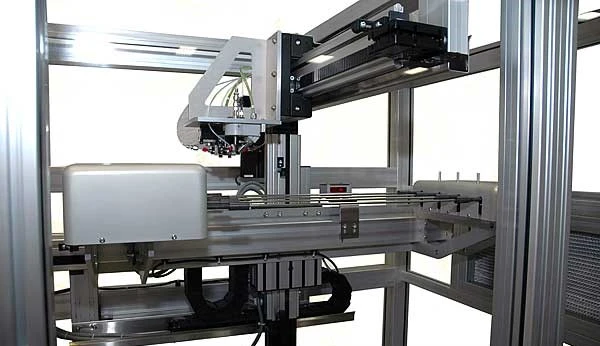
Spray Coating and Film Cast Equipment
Spray coating offers an alternative to dip coating for specific coating applications, products, and polymers. A variety of low-viscosity spray coatings can be applied in precision patterns to flat or multidimensional components. We’ve designed and supplied spray coating equipment for applications including medical devices, fuel cells, circuit boards, semiconductor wafers, solar photovoltaic products, and electronic display panels.
Our film cast equipment offers low- to medium-volume production rates for non-supported and supported films generated from liquid polymer solutions such as polyimide. Cast film equipment applications include wound care, drug delivery films, protective film, and electronics film production.
Our fully programmable control system allows for tracking and controlling subtle changes to key parameters. It also offers control and process monitoring as well as reliability for consistent performance.
Supporting coatings for a range of applications.
We can leverage our coating expertise to help you to identify the optimal coating for your molded or extruded product. In the medical device industry, coatings are often offered as value-added options for existing products as well as requirements for new products to achieve certain performance characteristics. Other industries that benefit from coatings include industrial, electronics, building, automotive, and consumer products. Coatings are commonly used to achieve enhanced resistance to wear, static or electrical current, environmental hazards such as moisture or UV exposure, or to provide features that the base material doesn’t offer, such as surface tack or reflective properties.
Types of Coatings
We work with you to select and apply the coating most appropriate to enhance your product’s surface and performance characteristics.
Lubricious Coatings
Lubricious coatings reduce friction and facilitate insertion. Products to which lubricious coatings are commonly applied include:
- Catheters
- Cannulae
- Guidewires
- Sutures
Silicone Coatings
Silicone Coatings
Used to reduce friction, these coatings can be applied to individual products or in bulk.
Products commonly coated with silicone include:
- Injection-molded products
- Metal devices, instruments, and components such as syringe needles
Polymer Coatings
These coatings provide a protective layer to enhance wear of a molded product or to protect a product that is exposed to moisture. A wide range of products are coated with polymers including:
- Scopes
- Sheath covers
- Surgical gloves
Drug-eluting Coatings
Medical devices can be coated to deliver drugs or hormones that are absorbed into the body. Products with drug-eluting coatings include:
- Stents
- Intrauterine devices (IUD)
- Sutures
Antimicrobial Coatings
Medical products with an antimicrobial coating can help to reduce risk of infection or irritation to skin or a wound area. Products with antimicrobial coatings include:
- Catheters
- Sutures
- Gloves
UV inhibitor coatings
These coatings are applied to materials such as glass and molded polymers that are subject to UV radiation; for example, coating glass vials that contain vaccines to increase shelf life when exposed to sunlight or fluorescent lighting.
Substrate Coatings
Fabric coatings
Coating a preformed shape, such as gloves, covers, and clothing, can provide a protective layer or a desired cosmetic appearance. Fabric coatings are also applied to enhance grip or provide hydration resistance for applications such as food or glass handling.
Metal coatings
Metal coatings often use polymers to help reduce friction, provide damping characteristics, or eliminate contact with sharp edges of stamped or formed metal products.
Paper & Cellulose Coatings
The food industry uses biodegradable coatings for food packaging. Coatings can also extend the life of utensils and food containers that come into contact with oils or waters.
Coated Products
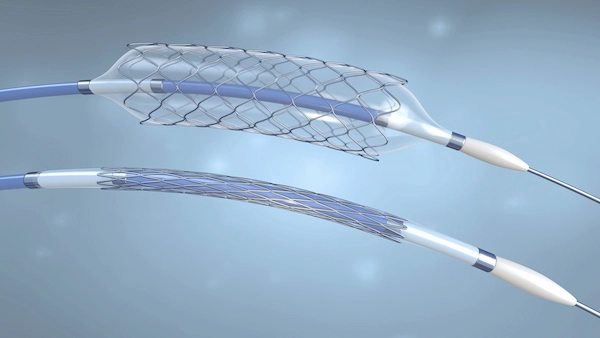
Cannulae & catheters
Medical devices commonly have lubricious coatings to minimize friction or antimicrobial coatings to reduce the risk of infection.
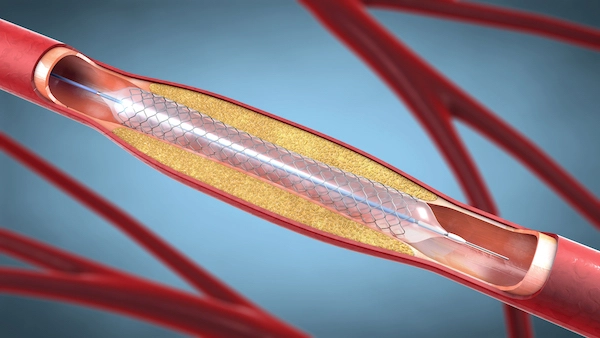
Stents & balloons
Drug-eluting coatings for medical devices allow the slow release of a drug to prevent complications. For example, cardiovascular stents can be coated with a drug that helps prevent blood clots. Angioplasty balloons can be coated with a drug to reduce the risk of future blockage.
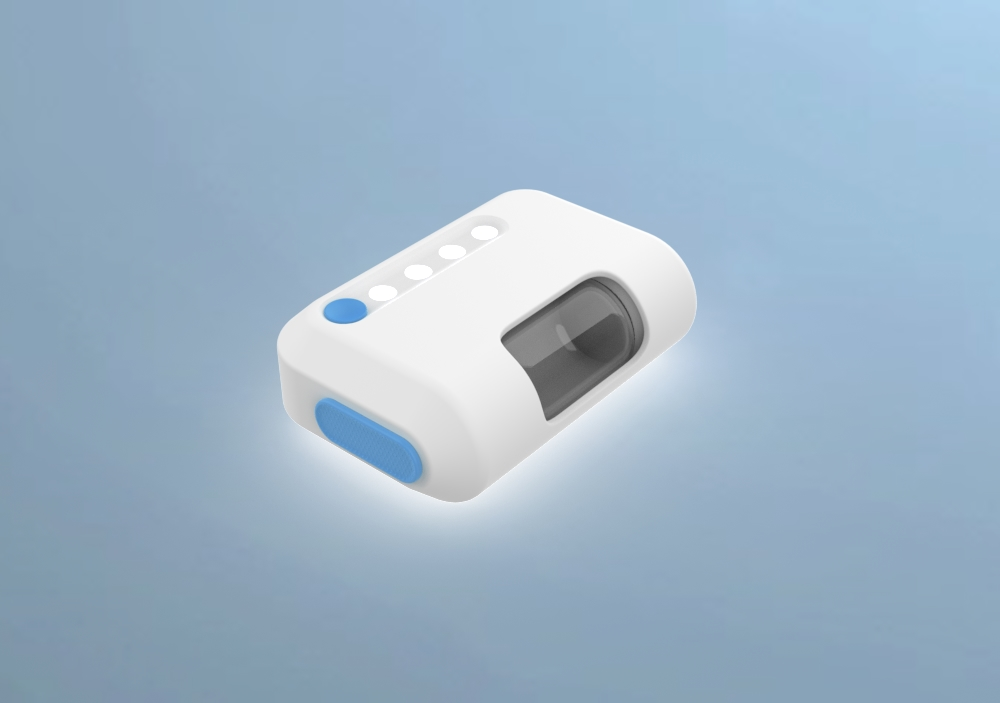
Silicone-coated injection-molded device
Silicone coatings are helpful in reducing friction in products such as autoinjector plungers or precision gears.