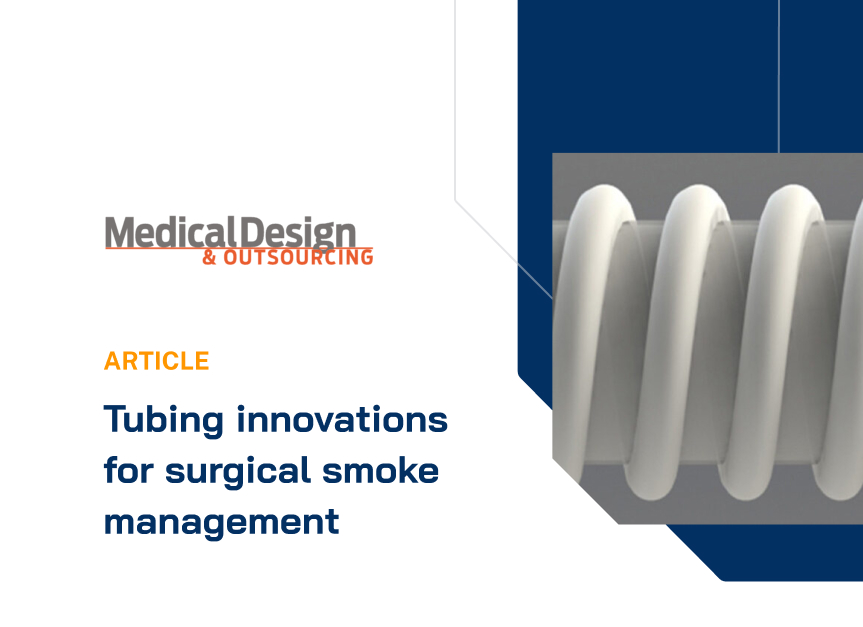
This article originally appeared in Medical Design & Outsourcing.
Tubing innovations for surgical smoke management
Device design with users in mind can increase adoption of smoke evacuation systems in operating rooms as new rules roll out.
By Martin Forrester, Aptyx
Anyone who’s observed a surgical procedure knows that smell. It’s surgical “smoke,” an umbrella term for a range of gaseous byproducts produced when tissue is dissected or cauterized by heat-generating devices such as lasers and electrosurgical pencils.
An estimated 500,000 surgeons, nurses, and other operating room (OR) staff are exposed to surgical smoke annually. The amount and content of smoke generated vary widely by type of procedure, surgeon technique, pathology of tissue and type of energy. But generally speaking, surgical smoke and aerosols are irritating to the lungs and have approximately the mutagenicity of cigarette smoke.
Expanding state legislation expected to increase demand
The National Institute for Occupational Safety and Health (NIOSH) and the Joint Commission both recognize the hazards of surgical smoke and recommend — but do not require — risk mitigation strategies including smoke evacuation systems.
In response to this lack of national regulation, the Association of periOperative Registered Nurses (AORN) has been working at the state level to enact laws that explicitly require hospitals and ambulatory surgery centers to implement policies requiring the use of surgical smoke evacuation systems. Currently, 18 states have passed laws specifically for smoke evacuation systems, and work continues in several more states.
With more than a third of U.S. states enacting laws for smoke evacuation systems and more likely4, increased demand for smoke evacuation systems provides opportunities for medical device manufacturers in this space.
Equipment design presents opportunities to boost adoption
Smoke evacuation systems typically have a suction unit (vacuum pump) that collects smoke, a filter to remove harmful particles and trap fluids, and tubing that connects the vacuum pump to the hand-held surgical device.
A review of 15 journal publications found that equipment design factors have historically presented a barrier to adopting smoke evacuation systems. Obstacles reported include bulky, noisy systems and heavy, awkward hand pieces. The tubing that links the suction unit to the surgical device often lacks flexibility and can compromise user experience by adding weight, pull force and resistance.
While equipment manufacturers have been working to make systems smaller and quieter, there are additional opportunities for innovation in smoke evacuation tubing to improve user experience.
Smoke evacuation typically uses smooth spiral tubing, which comprises a helix that spirals the length of a smooth-interior tube to support the hose and prevent it from being crushed, and a web that wraps around and between the helixes.
Some teams have tried substituting a lighter-weight, less expensive form of tubing known as corrugated; however, current corrugated tubing makes a whistling noise that can be distracting. While techniques for manufacturing quieter corrugated tubing are worth investigating, there are several innovative options available now.
In smooth spiral tubing, “pitch” is the distance between helixes. As tubing diameter decreases, so does the pitch. Decreasing the pitch makes the tubing more rigid, while increasing the pitch makes the tube more flexible.
Customer feedback inspires development of variable-pitch tubing
Variable-pitch tubing can increase a medical hose’s flexibility.
One recent process technique — in-line, variable-pitch tubing — was developed based on surgeon feedback that holding a device with smoke evacuation tubing caused wrist fatigue due to bending and articulating.
Some teams were even manually stretching out the end of the tubing close to the hand piece to give the tubing a lighter, more flexible feel. Stretching the tubing in an uncontrolled manner can damage the web and cause an inconsistent pitch, which could compromise tubing strength and performance.
Trials were conducted to discover the optimal amount of pitch variance needed to boost flexibility without compromising the pitch consistency needed to maintain strength. The result was the development of an automated in-line manufacturing and inspection process that varies the pitch along the length of the tubing.
For example, the end that connects to the vacuum pump could start with a 4 mm pitch, and the pitch could be increased to 6 mm at the device end of hose to enhance flexibility. This automated in-line process does not add cost to the tubing manufacturing process and ensures reliability, which is further enhanced by in-line inspection.
Additional opportunities for tubing enhancements
Dual extrusion allows for the helix and web of a medical hose to be manufactured from different materials.
Innovations from the respiratory tubing market can be leveraged for smoke evacuation applications. Through a patented process, tapered corrugated tubing can be fabricated with varying diameters within the tube. This tapered tubing features a standard diameter on the end that connects to the unit and thinner diameter that’s lighter and more flexible at the point of use.
Another example is an advanced manufacturing technique that embeds a wire under the helix in a very precise location to reduce condensation in respiratory tubing. This technology may offer potential for performance enhancements in the smoke evacuation space. For example, wires embedded in the tubing could be connected to sensors that would communicate with smart devices.
Extrusion materials and techniques offer additional opportunities for tubing advancements. Most smoke evacuation tubing is fabricated via single extrusion of one material. Dual extrusion — manufacturing the helix and web using different materials — presents an opportunity to optimize performance. For example, creating a highly flexible web with an extremely rigid helix, resulting in a lightweight, flexible hose that maintains structural integrity.
These are just a few examples of innovative opportunities in smoke evacuation tubing to boost performance and enhance user experience. Ultimately, these efforts will make ORs safer for patients and staff alike and will help protect the health of those who dedicate their lives to protecting the health of others.
Martin Forrester
Martin Forrester is a device industry veteran who served as R&D manager for Aptyx in Trenton, Ontario, Canada, for 25 years and continues to support Aptyx’s medical tubing R&D. He has specialized in tubing for more than 40 years and holds several patents that have been instrumental in many of Aptyx’s tubing innovations, including helically wound spiral tubing used for heated hose applications, strain reliefs and smoke evacuation applications.
This article originally appeared in Medical Design & Outsourcing.