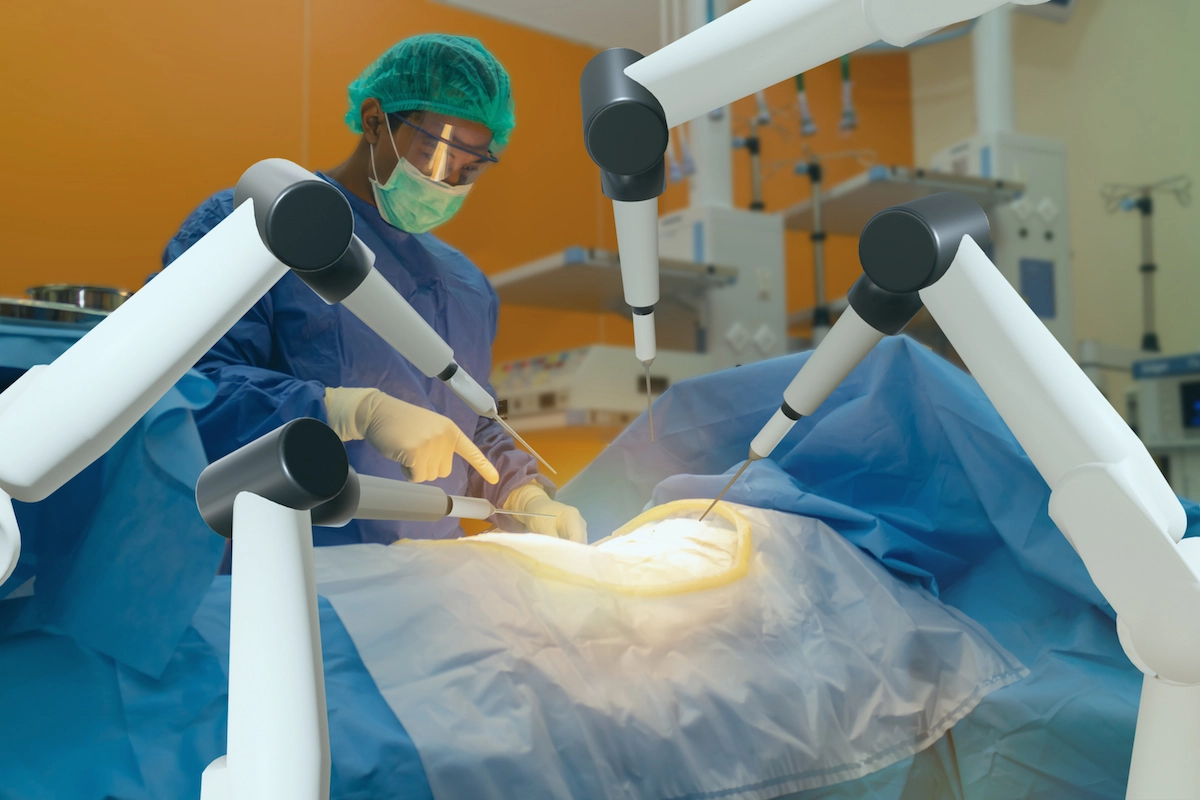
Customer Situation
A surgical robotics company partnered with Aptyx to develop 26 components over two phases for a next-generation robotic surgery system. The original gear assembly featured a brass gear with a stainless-steel shaft and over-molded two-part wheels. The labor-intensive manual process of pressing the shaft into the gear hub was costly, time consuming, and created quality issues. The original wheel had a machined hub that was hand loaded, over-molded with thermoplastic polyurethane (TPU), and manually trimmed to size.
The customer’s goals were to improve component quality and ensure consistent, timely delivery while reducing cost. They chose to work with Aptyx because of the company’s 70-year history of manufacturing precision gears and complex molding expertise, particularly with two-shot molding.
Aptyx Solution
For this project, Aptyx leveraged its expertise in polymer materials, gears, in-house mold design and build, along with injection molding, including insert and 2-shot molding, and process development by certified master molders. This was further supported by strong project management and quality engineering.
The Aptyx team used their depth of design for injection molding manufacturability (DFIMM) principles to modify the customer’s original design to accommodate injection-molded plastic components for the critical gear applications with over-molding a stainless-steel shaft and two-shot molding for the wheel.
Material selection is critical with high-performance, precision gears. The material changes required a thorough understanding of the application and the performance requirements, as well as the characteristics of polymer gears. Some factors the team considered included:
- The size, shape, and configuration of gear teeth and the critical gear-meshing interface
- Thermal expansion: how the axial and radial dimensions change in different temperatures
- The gear profile to ensure a smooth operation with good meshing
- Eliminating sharp corners that cause stress that leads to cracks or breaks
- The critical over-molding interface and torque requirements for the stainless-steel shaft
In Phase I, the modified wheel design featured an injection molded first shot polycarbonate (PC) hub with a second shot polyurethane coating. For this component, the Aptyx team adapted their two-shot molding machine and developed a process to first-shot the PC hub and then second shot over-mold the polycarbonate hub, which replaced a costly manual secondary handling operation. This eliminated the need for a machined inner hub, inspection, handling, over-molding and an expensive and prone to quality issues secondary trimming operation, which resulted in more than 80% cost savings.
The complex gears and wheels were injection molded with tight tolerances on the ID for bearing transition fits and OD press fits for the wheels on the gear hubs. The gears were molded from an Acetal polymer, a polymer ideal for applications that require high load-bearing capacity, resistance to deformation, lubricity, and smooth, quiet running operation.
In Phase II, the team was awarded complex components with tightest tolerances, which included additional cost saving improvements for several large, molded components. Numerous current production parts required expensive secondary machining operations to meet tolerances and the critical functional requirements. These larger parts required extensive Moldflow® analysis completed by both Aptyx and a third-party partner. In addition, these parts required extensive complex mold designs, which included multiple slide actions and insert areas along with planned tooling insert features to meet the tight tolerances. Finally, to ensure critical tolerances were met, Aptyx utilized their in-house metrology lab, including VMM’s and model based CMM with vision along with third party expertise for CT scanning inspection.
Outcome
The change from brass to polymer gears and the two-shot molded assembly resulted in dramatic cost savings of approximately 80%. In addition, the new manufacturing process resulted in shorter production times and better control of product quality due to fewer machining and subassembly operations.
“The Aptyx team did an excellent job converting the brass gears to plastic,” said the customer’s lead principal engineer. “Because of the design challenges, deep expertise in gears and over-molding was crucial. The team also converted an expensive, labor-intensive part with quality issues to two-shot molding, which dramatically reduced cost, improved quality, and easily met the production needs.”
“Aptyx came through for us because of very good program management and good technical expertise,” the customer said. “Their resources to support the project were key, including a large, experienced cross-functional team and strength in DFM. The team was very thorough and reviewed and completed the many details that many molders overlook. Their quality documentation was also very thorough and complete.”