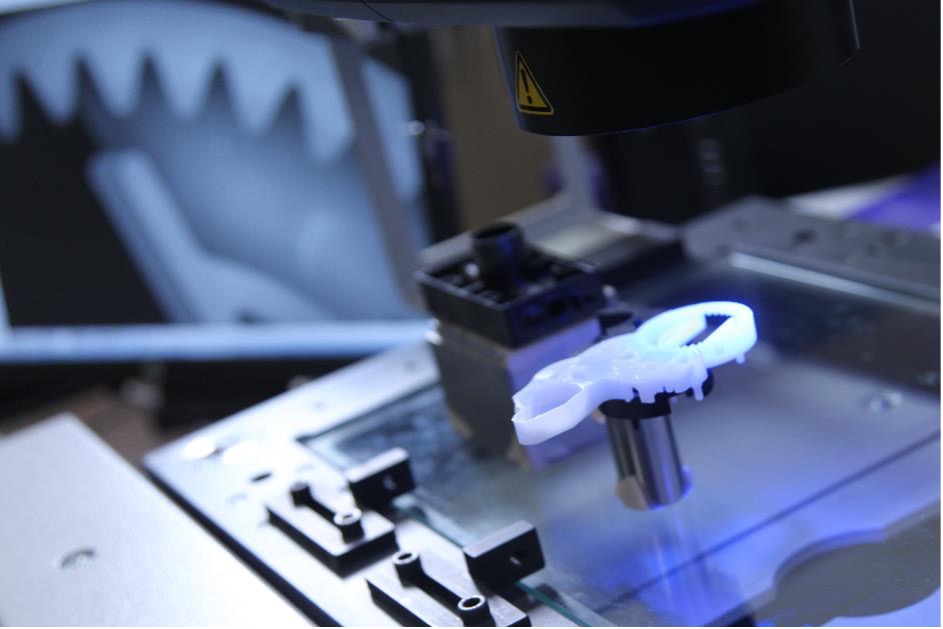
Plastic injection molding is a versatile manufacturing process that produces reliable, consistent products in a wide range of industries. Injection molding is equally suitable for precision medical devices and aerospace components as it is for children’s toys and decorations due to how reliable and precise it can be. When handled by the right team, like Aptyx, injection molding is absolutely indispensable.
In this blog, we will walk you through an in-depth guide to how the injection molding process works, and through each step, you’ll get a clear idea of why it’s so important to work with a reputable partner like Aptyx. We’re here to bring your plans to life with high-quality, cost-effective output.
Read on to learn more about the step-by-step injection molding process that will bring your product to life. If you are ready to partner with an industry leader in plastic processing, then contact Aptyx right away to connect with a member of our team to discuss how our custom plastic injection molding services can support your business.
The Benefits of Plastic Injection Molding
There are a lot of benefits to plastic injection molding, which is why it’s the standard manufacturing choice for countless industries. Here are just a few of the main benefits, but you can be certain that you’ll enjoy more benefits than those listed when choosing this process for your own manufacturing needs:
Cost Effectiveness
The first thing you’ll notice about plastic injection molding is that it’s very cost-effective, especially when you are doing a high-volume run. There is an initial investment for mold design and tooling, but once you are up and running, these costs are driven down very quickly by the remarkably inexpensive per-unit costs — even for incredibly intricate or complex pieces.
If you are planning to do a one-off, small production run, then it may not be worth the cost to go through mold design and tooling, but you’ll be surprised at how few units you’ll need to produce in order to offset the initial costs because of how reproducible and affordable each unit is. There is a significant reduction in labor costs alone, meaning that incredibly complicated pieces that could take hours and hours to produce by hand will be molded in a matter of seconds with perfect results.
Production Efficiency
A big part of injection molding’s cost-effectiveness is its production efficiency. When you use an injection molding process, you can produce significant quantities of parts in a very short time, and the quality is consistent and high-quality. For most injection molding processes, the time it takes to make a part is between a matter of seconds and a few minutes, depending on the size and complexity of the piece.
Injection molding is highly automated, reducing the risk of human error. It allows a producer to create parts on a 24-hour cycle without shift changes or downtime. By producing massive quantities of parts in a short time with reliable quality and cost-effectiveness, you can meet the market’s demand.
Complex, Detailed Pieces
Before injection molding, creating an intricate and detailed piece required a master craftsperson who would spend hours meticulously reproducing a part, and even then, there would always be inconsistencies across a run. Injection molding allows you to reproduce complex parts with continuous output and reliable consistency across the entire production run. In fact, injection molding allows for such tight tolerances and intricacies that they would be impossible to create otherwise, meaning that injection molding is central to advancing technology and allowing for increasingly complicated devices to make our lives easier.
Things like complex medical devices, aerospace components, and electronics are all impossible to create without injection molding.
Consistency
Plastic injection molding is also preferred because of the consistency of the quality of production. When you are doing a large product run, you need to know that you can rely on high-quality results to reduce your per-unit cost. A great injection molding partner like Aptyx will make sure that as few pieces as possible are rejected during quality control.
We use high-quality molds, maintain precision temperature and pressure control, and optimize our cooling rates to make sure that each part meets your high expectations without sacrificing efficiency and production speed.
How Injection Molding Works
Plastic injection molding is a manufacturing process that starts by melting thermoplastic resins that are injected into a pre-made mold under high pressure. This mold is customized for the part that is to be produced. The high-pressure injection is meant to ensure that there are no cavities or air pockets left. Once the mold is filled, the resin cools and solidifies with the help of channels that are designed for optimal cooling. (Optimal, in this case, depends on the part design, the materials used, and other factors). Once the part is cooled, it’s ejected into a receptacle, where it then goes through post-processing like polishing, trimming, or anything else that needs to be taken care of to get the exact piece you are looking for.
Take a look at the next section for a more in-depth explanation of the injection molding process.
The Steps of Plastic Injection Molding
High-quality plastic injection molding is a multi-step process that takes raw feeder plastic and transforms it into exact reproductions of your original design for a part. Each step of the process must go off perfectly to make sure that the end result is consistently well-made. Here are the essential steps to the process:
Material Selection
Based on the requirements of your product application, we need to decide which thermoplastic resin is going to best suit your needs. Whether you are looking for strength, flexibility, resistance to chemicals, or thermal stability, there are a variety of plastic options that we will need to consider. The most common include polyethylene (PE), polypropylene (PP), acrylonitrile butadiene styrene (ABS), and polycarbonate (PC), but there are many other options, including engineered materials, such as Nylon, Acetal, PEEK, and Ultem that we will consider with you. It’s also essential that the material we choose is compatible with the design of your mold to ensure that we are producing optimal parts.
This selection process is all part of the engineering, molding, and manufacturing solutions we offer at Aptyx.
Mold Design
You have your part, and now it’s time to create a mold that will reproduce it reliably. We will take your detailed 3D CAD and 2D prints and factor in a variety of other variables, like the flow rate of the plastic being injected, the cooling rate of the type of plastic, and the way the part will need to be ejected safely. The mold will need to accommodate all of your requirements, including any tight tolerances or complicated design features.
A high-quality mold will produce advanced, consistent parts, but that’s not the end of the process.
Melting and Injection
The mold is designed and we’ve selected the right material, so it’s finally time to start the injection process. The thermoplastic resins are heated in a barrel until they are melted, and are then mixed to homogeneity. Once they are appropriately mixed, the plastic blend is injected into the mold at a very high pressure. The pressure ensures that the plastic doesn’t leave any air pockets, so each intricate detail and piece of the design is filled.
Cooling
The molten plastic will begin to cool and harden as soon as it is injected into the mold, but cooling too quickly or slowly can cause major issues with the final piece. The mold is designed with cooling channels that will help the material cool at the right rate to avoid brittleness, warping, marks, cracks, or other issues that can come in the cooling phase.
The cooling time will vary depending on the thickness of the piece, the material used, the design of the mold, and countless other factors that we will make sure to optimize for you.
Ejection
After the cooling phase, the mold will open so the part can be removed. There are a lot of different options for ejection, such as pins or plates that push the piece out of the mold into a catchment. As you can imagine, fragile or intricate parts are at risk of damage during the ejection, so we take care to design and control this step to avoid leaving marks or causing other problems.
This step is typically automated like the rest of the injection process, but we customize each ejection phase depending on a multitude of factors specific to the part, the material, and more.
Post-Processing
Once the part is ejected, there may need to be a few extra steps to make sure that each piece meets your rigorous standards of precision and quality. There may be some trimming necessary to remove extra materials, additional assembly of multiple parts, painting, or treating the surface.
Whatever is required for the post-processing of your part, Aptyx will make sure that you are getting exactly what you expect as our valued customer.
Are You Ready For Your Own Injection Molding? Contact Aptyx Today
Plastic injection molding is a versatile, efficient, and cost-effective manufacturing process that will ensure that your parts are of excellent quality, no matter how complicated they may be. At Aptyx, we specialize in high-volume, top-notch injection molding services that are customized to your needs. Contact us right away to learn more about the services we offer and to discuss your custom manufacturing goals.