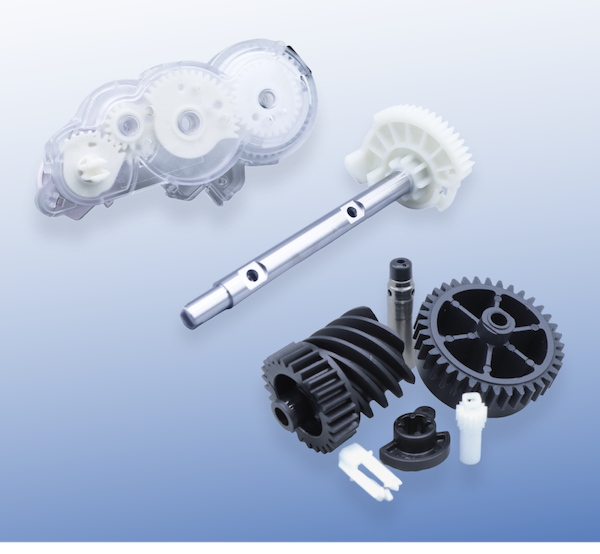
This post is adapted from an article that originally appeared in Design News.
For many devices, converting metal components to plastic is an effective way of enhancing product performance while driving down costs. Gears are a great example of a metal-to-plastic conversion that can reap many benefits for both the design engineer and the end user.
Here’s what to consider, whether you’re converting from metal to plastic gears or designing gears for a novel device.
Potential benefits of converting metal to plastic gears
1) Cost effectiveness & speed to market
Plastic gears generally offer both a lower material cost and a lower tooling cost compared with metal. The plastic injection molding process allows multicavity tools that enable more parts per shot, increasing throughput. An injection mold also can be built for multiple processes, such as insert molding, overmolding, and two-shot molding, which can eliminate the need for secondary operations.
2) Performance
With the trend toward miniaturization in medical devices, lighter-weight plastic materials are an attractive choice, particularly for technology such as wearable drug delivery devices. Weight is also a significant driver in the automotive industry, where design engineers are continuously challenged to reduce weight to meet tough fuel economy standards.
3) Quality & reliability
The injection molding process provides built-in reliability and consistency. Injection-molded gears often meet specifications right out of the mold, minimizing the need for extensive post-processing or adjustments. Integrating other molding processes into the mold—such as adding tabs or holes—reduces the risk of flaws and imperfections that can occur with secondary operations.
4) Flexibility of design
The injection molding process offers unparalleled flexibility in gear design, including complex gear shapes, intricate geometries, and holes.
Key design considerations for plastic gear conversion
While the primary driver of metal-to-plastic conversion is the application and its requirements, here are some related factors to consider.
1) Environment
Environmental considerations include:
- Thermal expansion
- Effects of moisture
- Effects of chemicals, corrosion and abrasion
2) Resin choice
With options ranging from traditional acetals, nylons, and polyesters to highly engineered materials such as Ultem®, Radel®, and PEEK, engineers have a vast toolbox of resins to accomplish desired performance characteristics. Resin considerations include:
- Weight
- Strength
- Lubricity/surface finish
- Temperature fluctuation
- Fatigue life
- Interaction with chemicals
3) Manufacturing methods
Injection molding operations such as insert molding, overmolding, or two-shot molding may be required to manufacture complex gear designs efficiently and cost effectively. Secondary machining operations may be necessary for integrating components such stainless steel pins or bushings.
4) Cost targets
Injection molding is a highly cost-effective process. Once you’ve invested in the mold, you can make parts relatively inexpensively.
Consult with our experts about plastic gear conversion
When considering a metal-to-plastic conversion, it’s important to work with a partner that understands the intricacies of designing and manufacturing plastic gears for advanced life science applications, motion control, and automation. Considerations should include not just cost, but the gear environment, resin choice, and manufacturing method to best meet the needs of the application.
By leveraging the cost-effectiveness, performance, quality, and design flexibility of plastic gears, design engineers can better meet the demands of increasingly complex, technology-driven innovations.