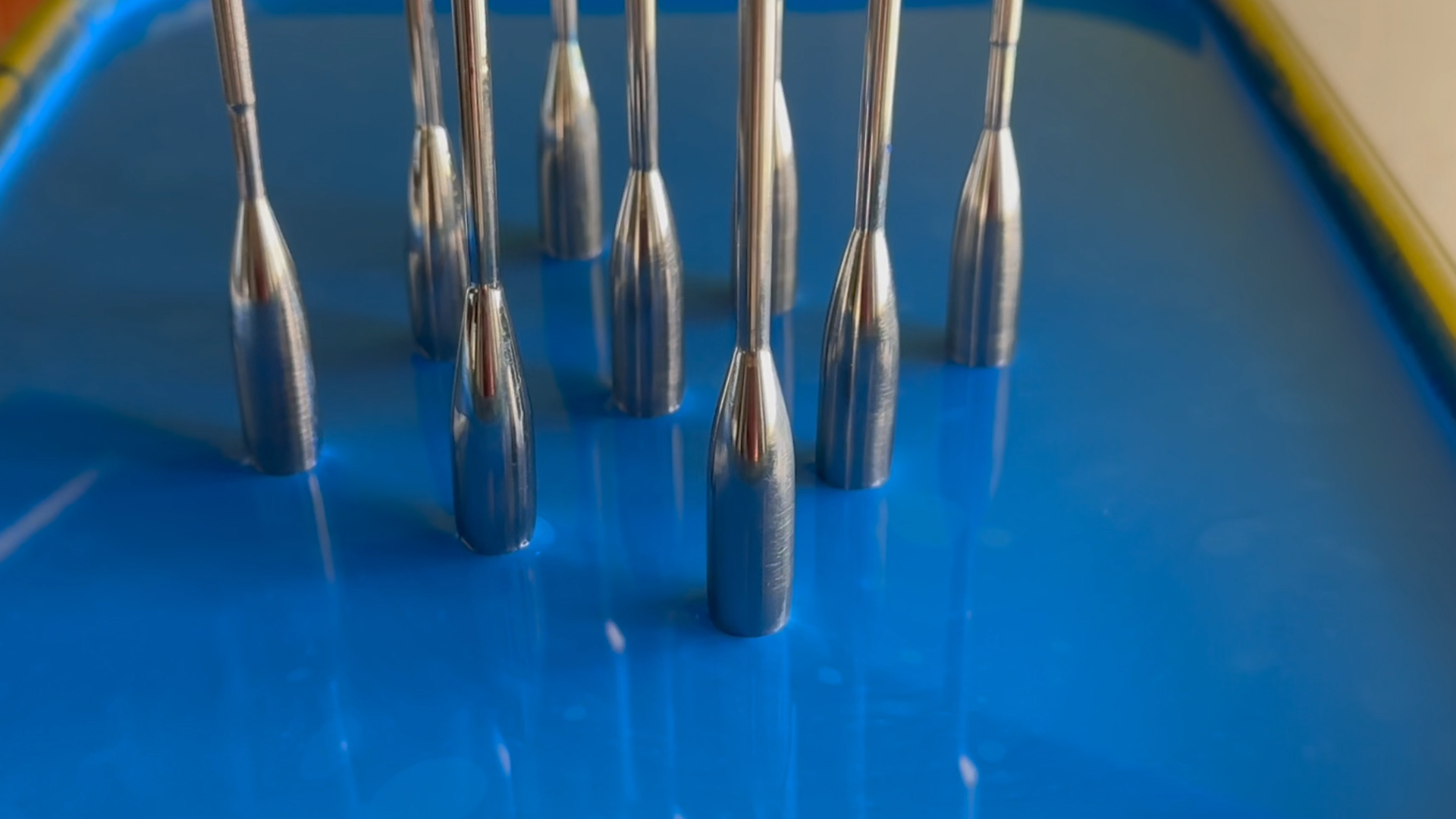
Product design engineers are all too aware of the importance of choosing the right materials, components, and processes to ensure the successful outcome of their product. And when it comes to scaling, these elements can determine the success or failure of the entire enterprise. Now, factor in the exacting standards of the medical device and life sciences industries, and you realize that there is very little margin for error.
Aptyx partners with manufacturers to develop solutions for complex processes. Whether you require molding, extruded tubing, tooling or custom dies, coating processes, or some other solution involving plastics or plastic production processes, your company can only benefit from our decades of experience in the industry.
Understanding Different Molding Processes
Aptyx currently utilizes over 300 plastic processing machines to produce components and finished devices for our clients. We have a broad understanding of the technology, molding process options, and machinery that our customers require. We partner with your in-house experts to design superior processes that improve quality and performance while optimizing cost.
This overview of the types of processes that we employ will demonstrate how we can integrate our services into your operations.
Injection Molding
If you require a particularly high volume of complex parts, our plastic injection molding services may be your preferred course of action.
How Injection Molding Works
The manufacturer selects the type of plastic suitable for the devices or components in question. This plastic is fed into the hopper, where they are led into a barrel. The barrel melts the plastic at the prescribed temperature. A screw attached to a plunger forces the liquified plastic into the mold, which consists of a cavity and core. Pressure is applied to ensure proper density and consistency. Afterward, the products are allowed to cool and can be cleaned, polished, or moved onto another step in the manufacturing process.
Advantages of Injection Molding
Among the benefits of injection molding are:
- It’s a flexible process that can be used for a variety of different parts constructed from various materials. In other words, if you have multiple components constructed from different grades of plastic, this process allows you to alternate between them by utilizing sub-processes such as overmolding, two-shot molding and insert molding.
- It’s easy to automate, which means that once it’s set up and tested, you can scale it up to continuously produce a high volume of products without extensive labor.
- Injection molding has a high rate of consistency as long as tight parameter controls are employed.
- This is a very cost-effective process. After the initial cost outlays of the tooling, the variable costs are relatively low when compared to other molding processes.
- Overall quality is high, which is one of the reasons why injection molding is such a popular option in the medical device industry.
When to Use this Process
Injection molding is suitable when the manufacturer requires a high volume of complex parts made from various thermoplastic resins.
Blow Molding
When you need to produce a thin-wall, hollow component, like a balloon, cuff, bottle or other container, blow molding may be the ideal solution.
How Blow Molding Works
A preform or parison, which is a plastic tube, is heated to the point where it’s about to melt and then fed into the cavity of the mold. Instead of a core pushing it into the walls of the cavity, as is the case with injection molding, compressed air evenly forces it against the walls. As the plastic cools, it retains the shape of a cavity. The result is a smooth, consistent, thin plastic product.
Advantages of Blow Molding
For a specific product type, blow molding has several benefits:
- There is very little waste product in blow-molding, meaning that manufacturers have lower material costs.
- It’s ideal for unusual shapes and contours since the plastic is blown to the shape of the mold.
- Finished products are literally seamless. Contrast this to a hollow component that has to be assembled from two or more parts.
- The blow molding process can use many materials, including HDPE, PP, PVC, TPE, PET, and more.
When to Use this Process
This process is ideal when you require products or components that do not require thicker walls. However, it is also not as precise as injection molding, so it is less than ideal in situations where the components have fine details or must mesh perfectly with other parts. If you require a large volume of hollow components, blow molding may suit your needs.
Dip Molding
Dip molding is particularly useful for products and components that do not require rigid plastics, where there may be less need for precision, or may have a unique geometry.
How Dip Molding Works
Dip molding involves dipping a metal substrate in a precursor solution and then into a tank of liquified polymer or elastomers, typically plastisol but other materials can be used. When the substrate is removed from the tank, it cools, and the polymer products can then be removed from the substrate. In a process similar to dip molding, known as dip coating, components or devices can also be coated with a polymer.
Advantages of Dip Molding
For certain products, the benefits of dip molding are numerous:
- With all other things being equal, dip molding is the least costly of the molding processes we’ve discussed here.
- Dip molding can be used in numerous instances to create elastic polymer parts or supplies with no seam or parting line. For example, dip molding can be used to create cannulae, latex gloves, stethoscope tubing, rubber grips, and more.
- Dip molding allows the creation of complex geometries such as a Y shape and has the flexibility to change wall thickness even after tooling is built.
- There is little waste since excess material remains in the tank.
- Unlike some of the other molding methods, dip molding makes sense even for low-volume production.
- Dip molding is compatible with softer materials, like latex, nitrile, silicone, etc.
When to Use This Process
Dip molding is often the right process for products and components that don’t require the level of durability and precision that injection molding offers.
Before you commit to any particular custom molding solution for your product or processes, contact Aptyx. Our engineers have a vast amount of experience helping companies design processes. We can make recommendations to improve your processes and avoid unnecessary costs.
Factors to Consider When Choosing a Molding Process
While most projects require a bespoke approach when it comes to molding, having an idea of the needs of the project can help you avoid costly errors and delays when you’re developing your processes or partnering with us to develop the process.
The following factors will influence the type of molding selected.
Material Selection
Consider these factors when selecting plastics for your components or products:
- Will the plastic interact with chemicals or cleaning solvents?
- Will the plastic component be exposed to extreme temperatures or moisture?
- What level of flexibility is required? For example, a stethoscope tubing must be flexible, but the housing of a medical machine should be rigid.
- What level of force or torque must it withstand?
- Whether the part is intended for reuse or is disposable and if reusable, what is the expected lifetime?
- How well does the material withstand the molding process?
- Will you be adding dyes or other adulterants to the plastic material?
- What are the material costs of different types of plastic? Would a cheaper material work just as well without increasing other costs?
If you have any questions regarding plastic materials, contact us. We can make recommendations and help you to avoid difficult-to-see pitfalls.
Production Volume
Your anticipated production volume can have a significant impact on your decisions about molding processes, materials, and the overall viability of the project. You may have relatively moderate manufacturing goals at the moment, but scaling should always be part of a design vision. All of the aforementioned processes can be scaled up with relative ease, but depending on the process and the specialization of the equipment, downward scaling may be more difficult. Our engineering team can discuss the various challenges you face with regard to production volume and scaling. Ultimately, it may be in your best interest to outsource the production of a component to our facilities.
Part Complexity and Design
As a rule, complex parts often require harder plastics. This usually means injection molding. Hollow parts can often be accomplished with our custom blow molding services. Dip molding may be the best and most affordable way to go when the plastics involved are softer and simpler.
If you require a seamless finish, it can also influence the process and materials that you select.
Cost and Budget Constraints
Aptyx is known for finding the most cost-effective processes and materials for our partners’ projects. We will only suggest processes and materials that meet the requirements of your project. If there is a more affordable and effective way to achieve the same results, we will uncover it. We offer injection, blow, and dip molding services and can support you end-to-end in your development and manufacturing needs.
Aptyx employs over 1,000 highly trained scientists, engineers, and other plastic manufacturing experts. Across our global network, we have facilities that are ISO 13485-2016 and FDA registered, which is why so many medical device and life science manufacturers turn to Aptyx. Contact us to discuss your plastic molding requirements.